Repairs and Warranties You Can Count On
If your tools encounter any issues, our fast and reliable repair services ensure minimal downtime and maximum durability. With our comprehensive warranty and expert repairs, we help extend the life of your equipment, so you can focus on getting the job done right.
Repair
Explore the comprehensive warranty and repair services offered for our torque tools.
In the event of any issues, our efficient repair services guarantee a swift resolution, minimizing downtime and maximizing the longevity of your tools.
Explore the comprehensive warranty and repair services offered for our torque tools.
In the event of any issues, our efficient repair services guarantee a swift resolution, minimizing downtime and maximizing the longevity of your tools.
All repairs are done on-site in our Carol Stream, IL factory.
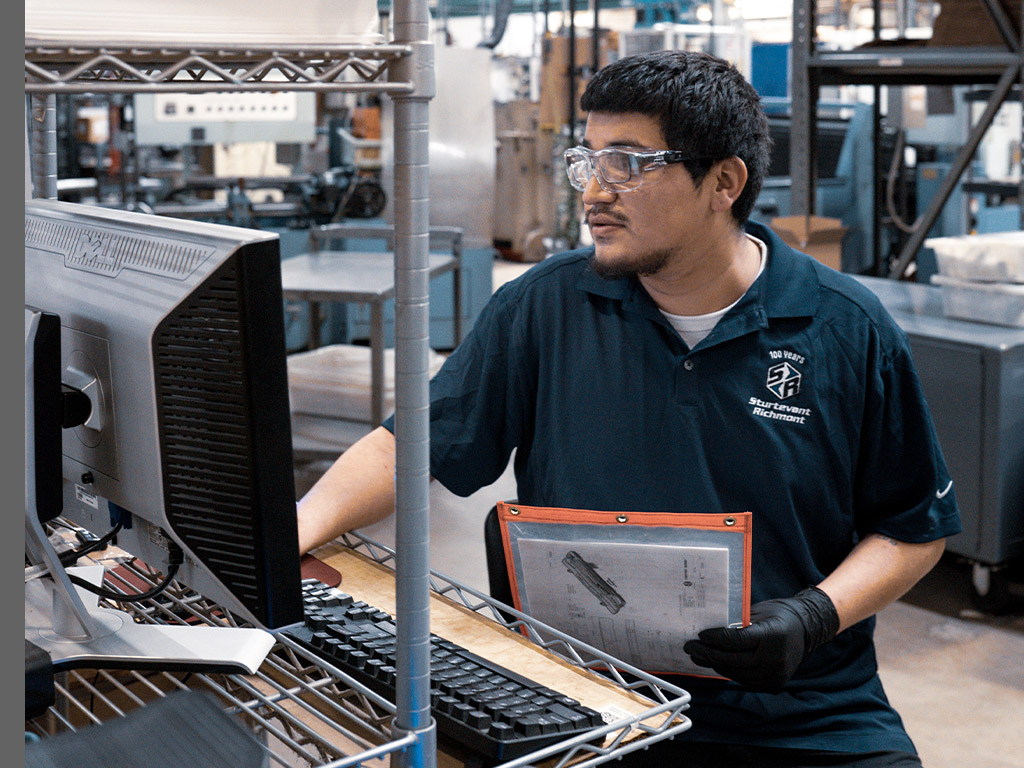
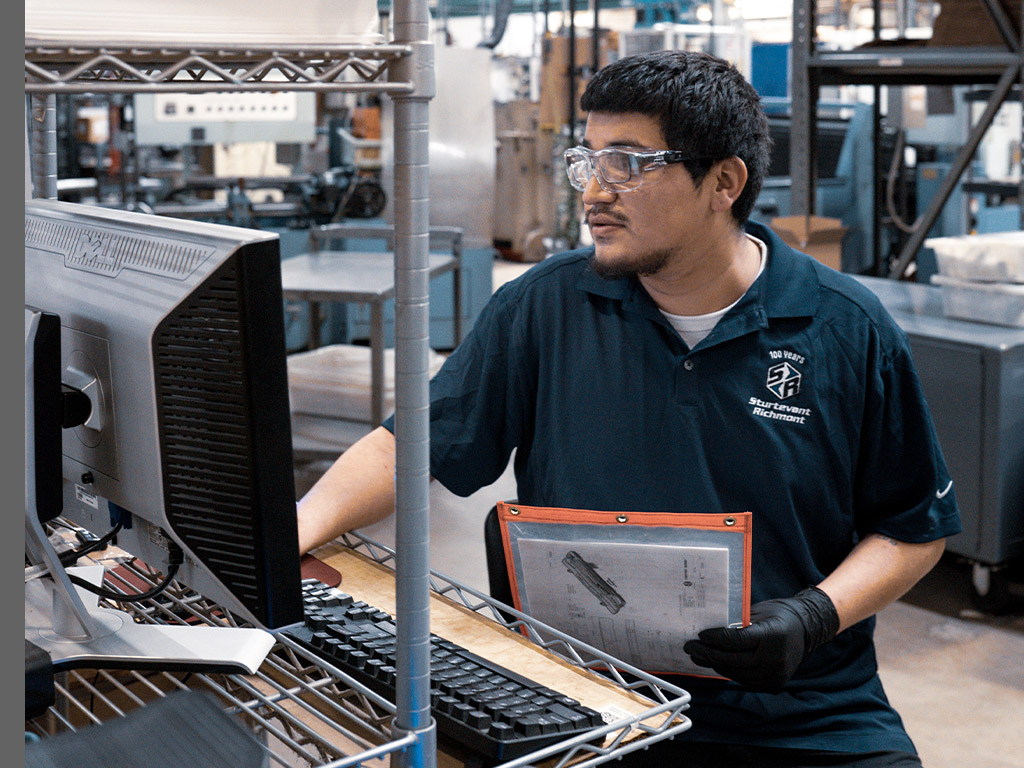
Do your tools
need repair?
We can help. Start here:
Request the Form: Email [email protected] to receive the calibration/repair form
Complete the Form: Provide a detailed description of your requirements and repair needs
Schedule Calibration: Email the completed form back to [email protected] to schedule your service
Ship Your Tools: Print a copy of the form and include it with your tools or tester when shipping them to us
A RGA (returned goods authorization) is not required for repair work. There is a fee for repair diagnostic. That fee is applied to the cost of the repair.
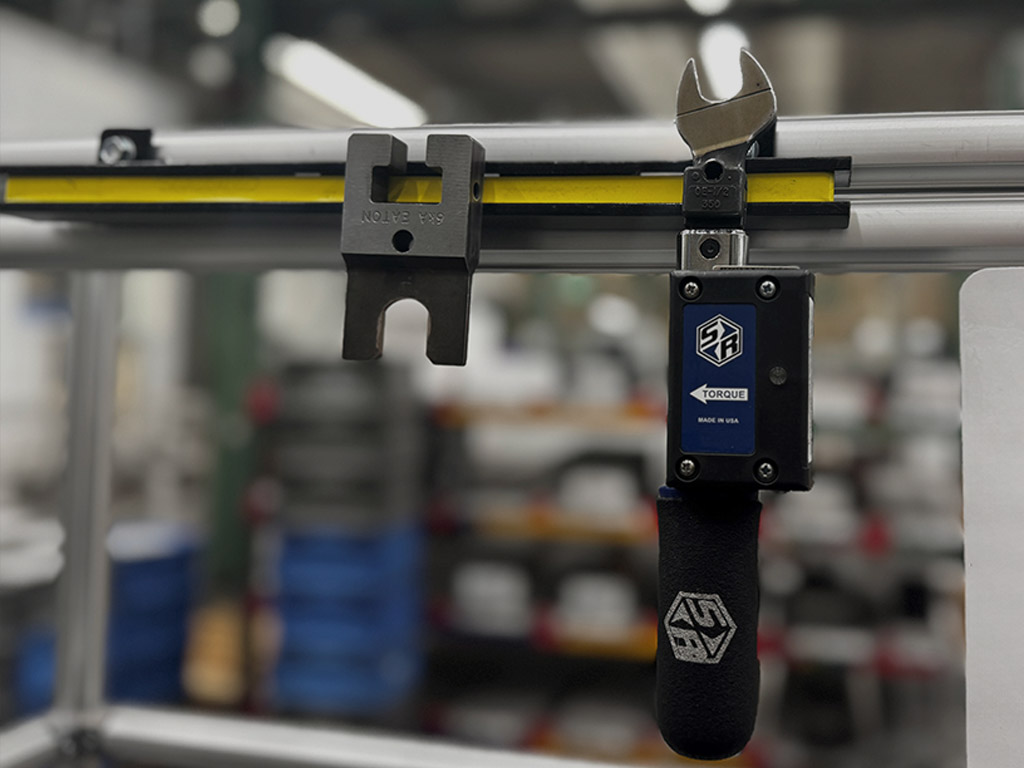
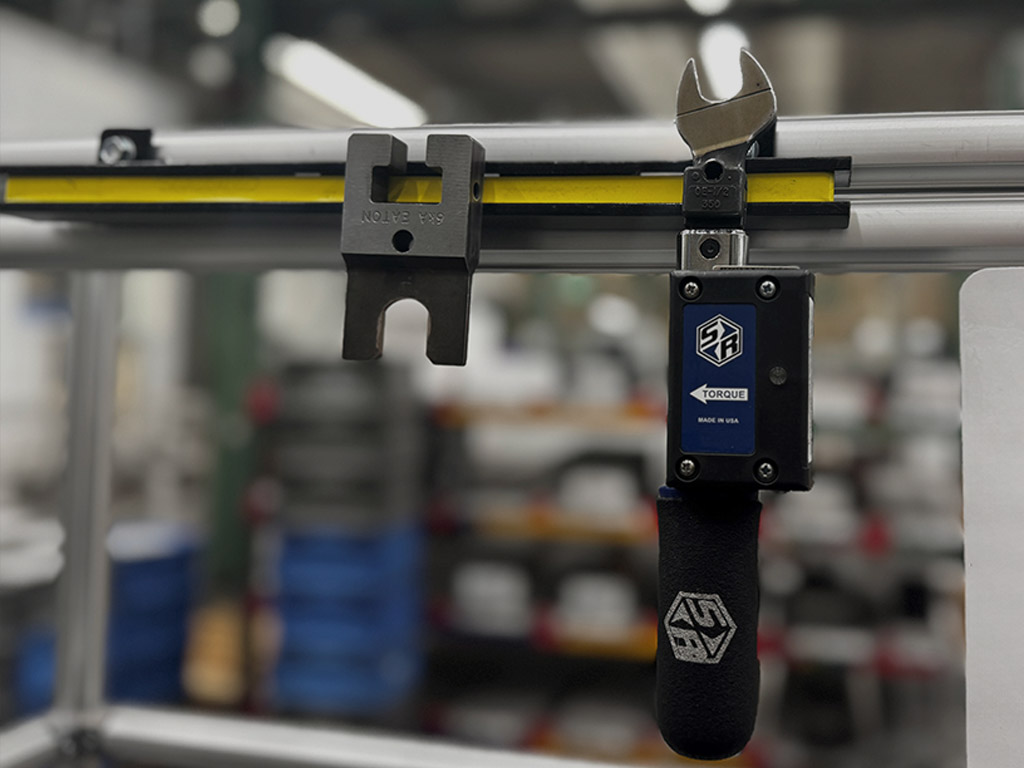
Sturtevant Richmont Limited Warranty
Sturtevant Richmont warrants all products in our catalog against defects in material and workmanship for the periods outlined below. Upon inspection, Sturtevant Richmont reserves the right to either repair or replace the defective product at our discretion. This repair or replacement, provided at no charge to the customer, shall be the customer's sole and exclusive remedy under this warranty. This limited warranty supersedes all other warranties, whether express or implied, including any warranties of merchantability or fitness for a particular purpose.
Warranty Exclusions
This warranty shall be void for any products that are damaged or rendered unserviceable while in the custody of the customer or third parties. This includes, but is not limited to, damage caused by negligence, misuse, modification, unauthorized repair, or altercation of the product.
Warranty Coverage
While we are committed to providing high-quality products crafted with precision and expertise, this warranty does not cover damages resulting from misuse or abuse. For example, exceeding the product's stated capacity immediately voids the warranty.
Battery Requirements
Certain tools, including the Exacta 2 Torque Wrenches, DTC Series Torque Wrenches, TAC Wrench, and Digital Torque Testers, feature advanced electronics that require NiMH battery power. Use of any batteries other than the prescribed NiMH batteries will immediately void the warranty.
Warranty periods
All time periods are from date of purchase
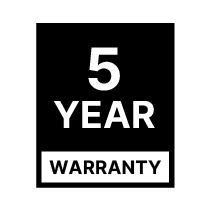
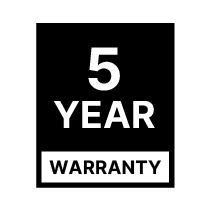
Mechanical Loading Systems
Calibration Arms
Load Platforms
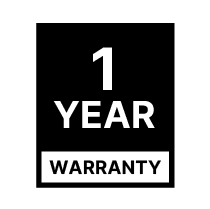
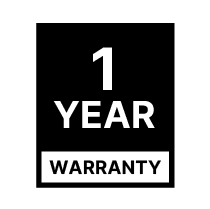
Torque Transducers
Torque Testers
All other products
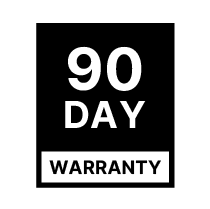
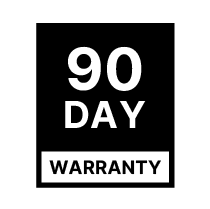
Software
Calibration