About
Built for Precision, Trusted for Performance
At Sturtevant Richmont, we specialize in transforming challenges into simple, efficient solutions. Your quality is our business.
Accurate. Reliable. Durable. It's more than just a promise; it's the foundation of everything we do.
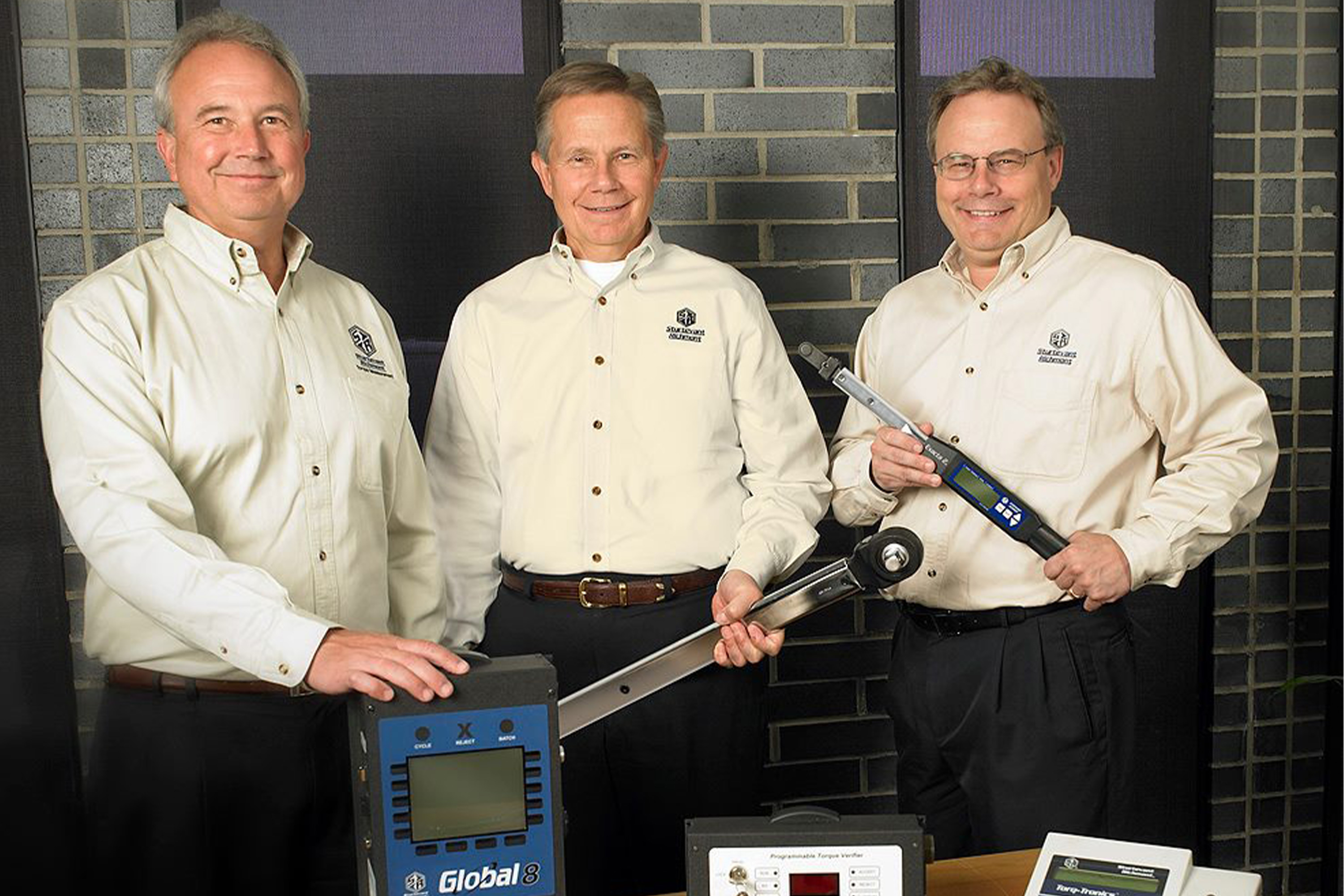
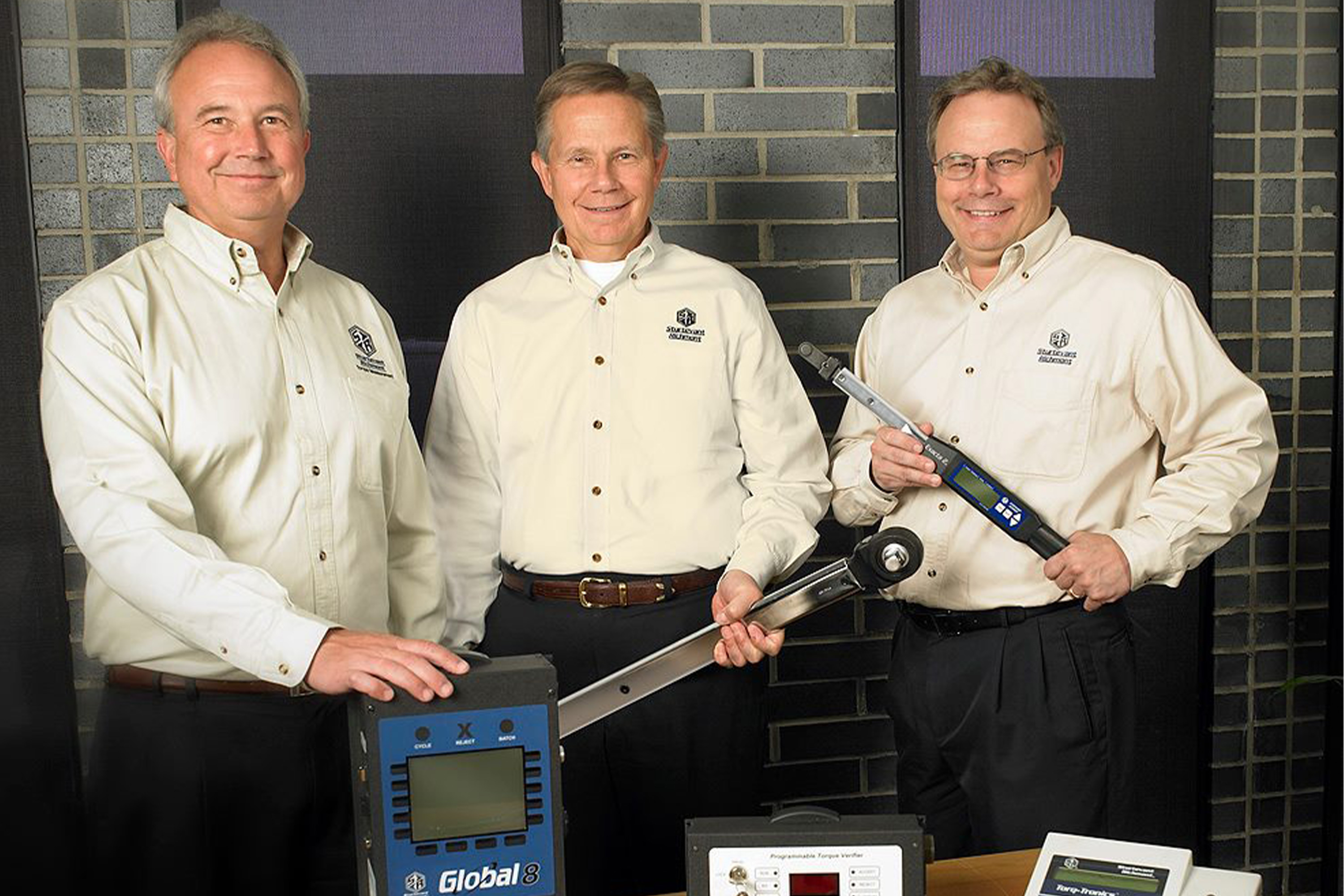
Dependable tools,
decades of innovation
With over 100 years of innovation, Sturtevant Richmont leads the way in torque tools. Born from the merger of two industry pioneers - Paul Sturtevant and Frank Livermont - we've set the standard with patented designs and advanced error-proofing systems. Now under the leadership of John Reynertson and as part of the Snap-on family, we remain dedicated to building on our heritage of innovation and expertise. As torque tool specialists, we continue to push the boundaries of technology and precision, delivering high-quality products that meet the evolving needs of industries worldwide. While our reach has grown, our focus on craftmanship, reliability, and customer satisfaction stays the same, ensuring that we remain your trusted partner for torque solutions for years to come.
Committed to your success
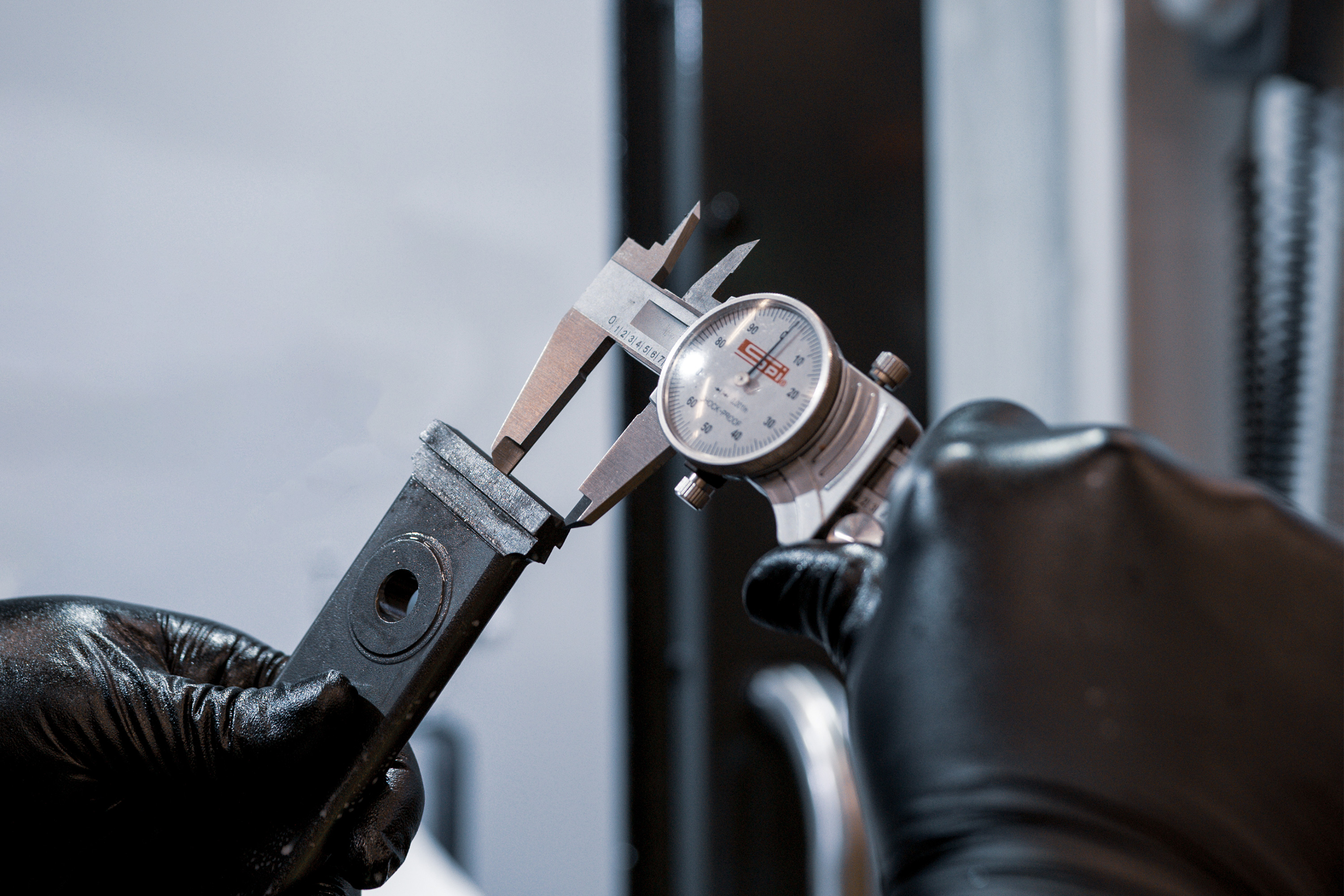
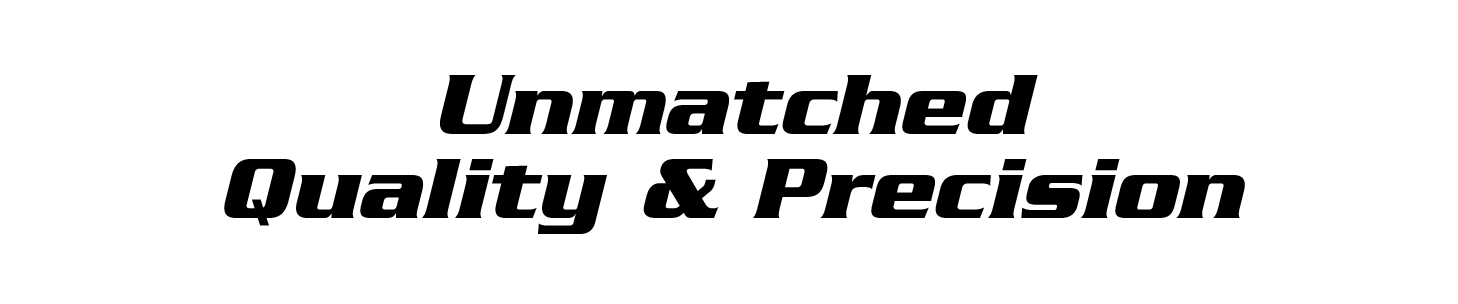
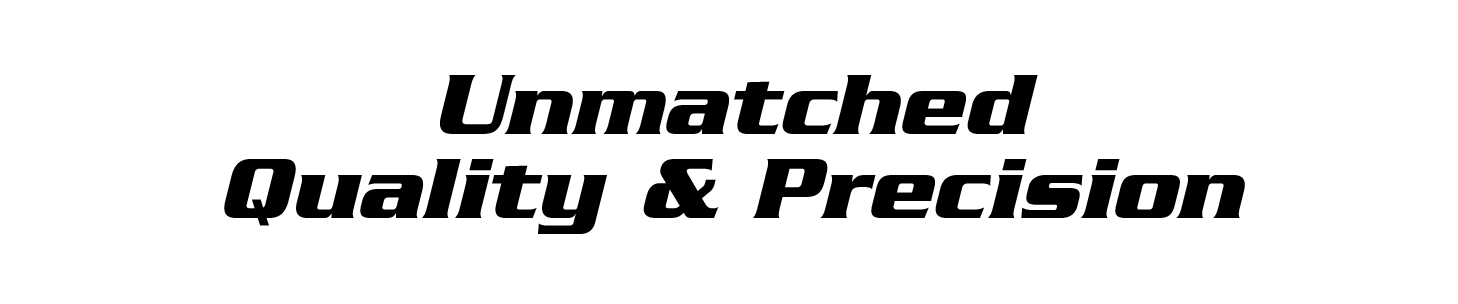
Sturtevant Richmont tools are known for their exceptional accuracy and durability, backed by superior materials like aerospace-grade aluminum and high-grade steel. Our meticulous design ensures better calibration and long-lasting performance.
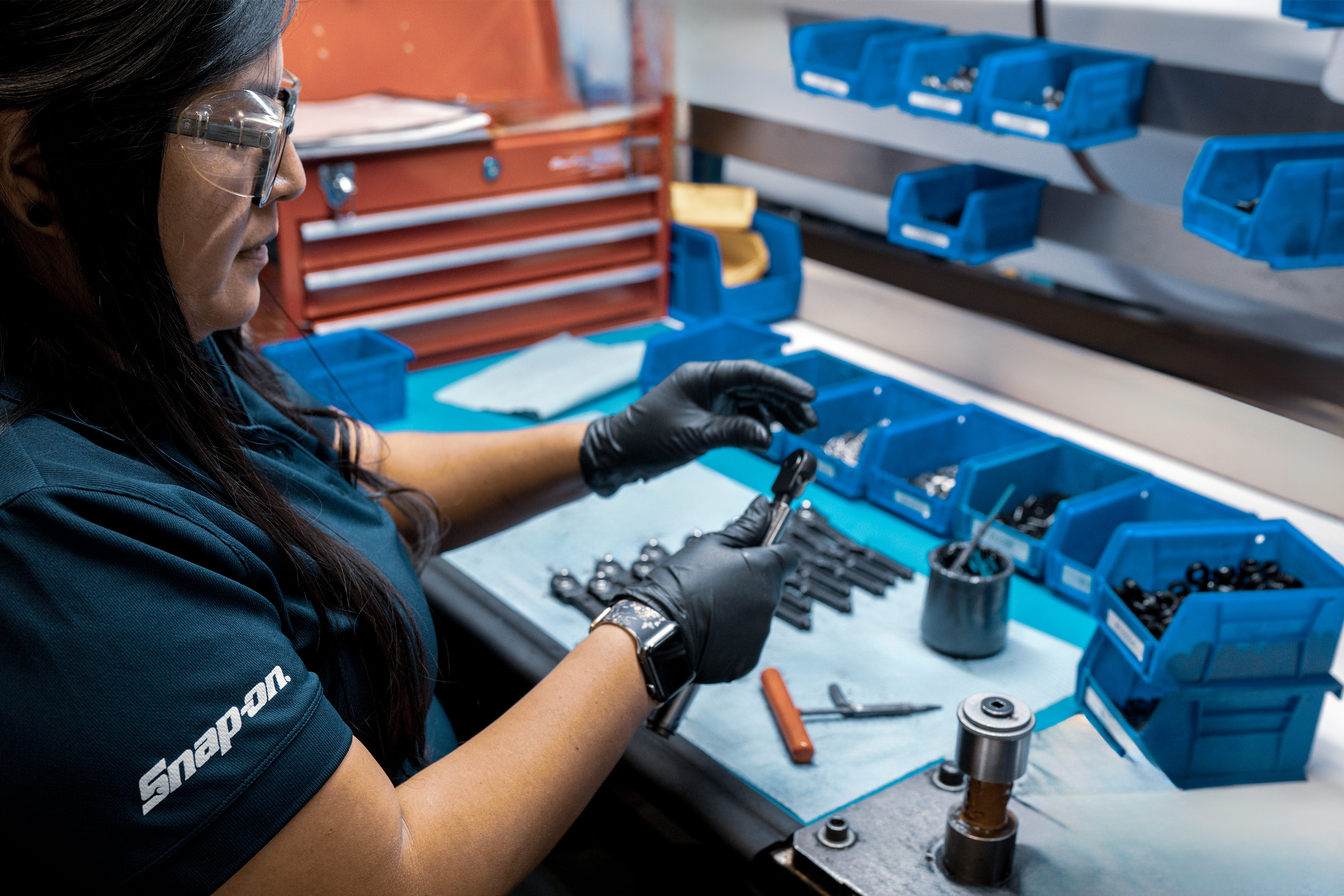
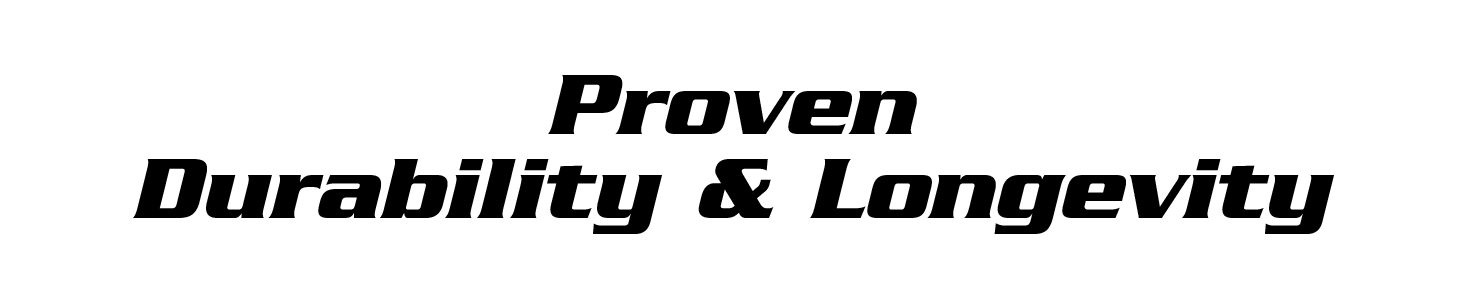
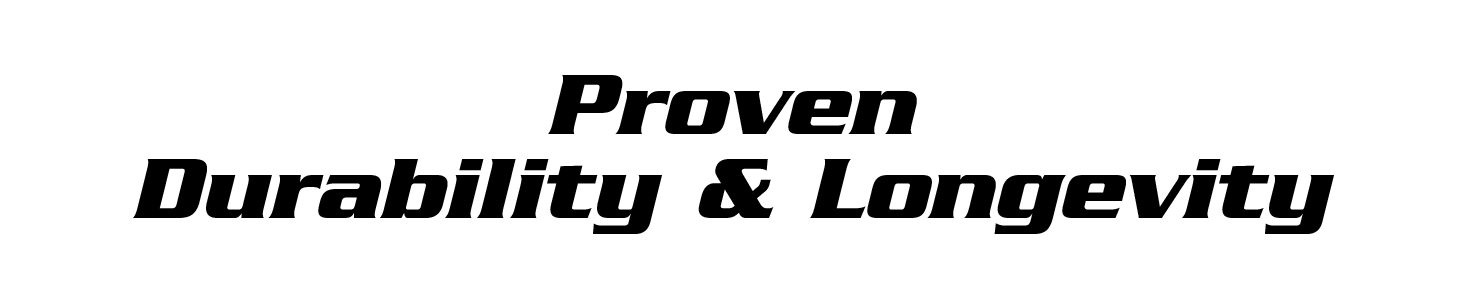
Sturtevant Richmont tools are built to last. Many of our products continue to perform reliably for decades. With a legacy of long-term use, our tools deliver enduring value, making them a wise investment for consistent performance over time.
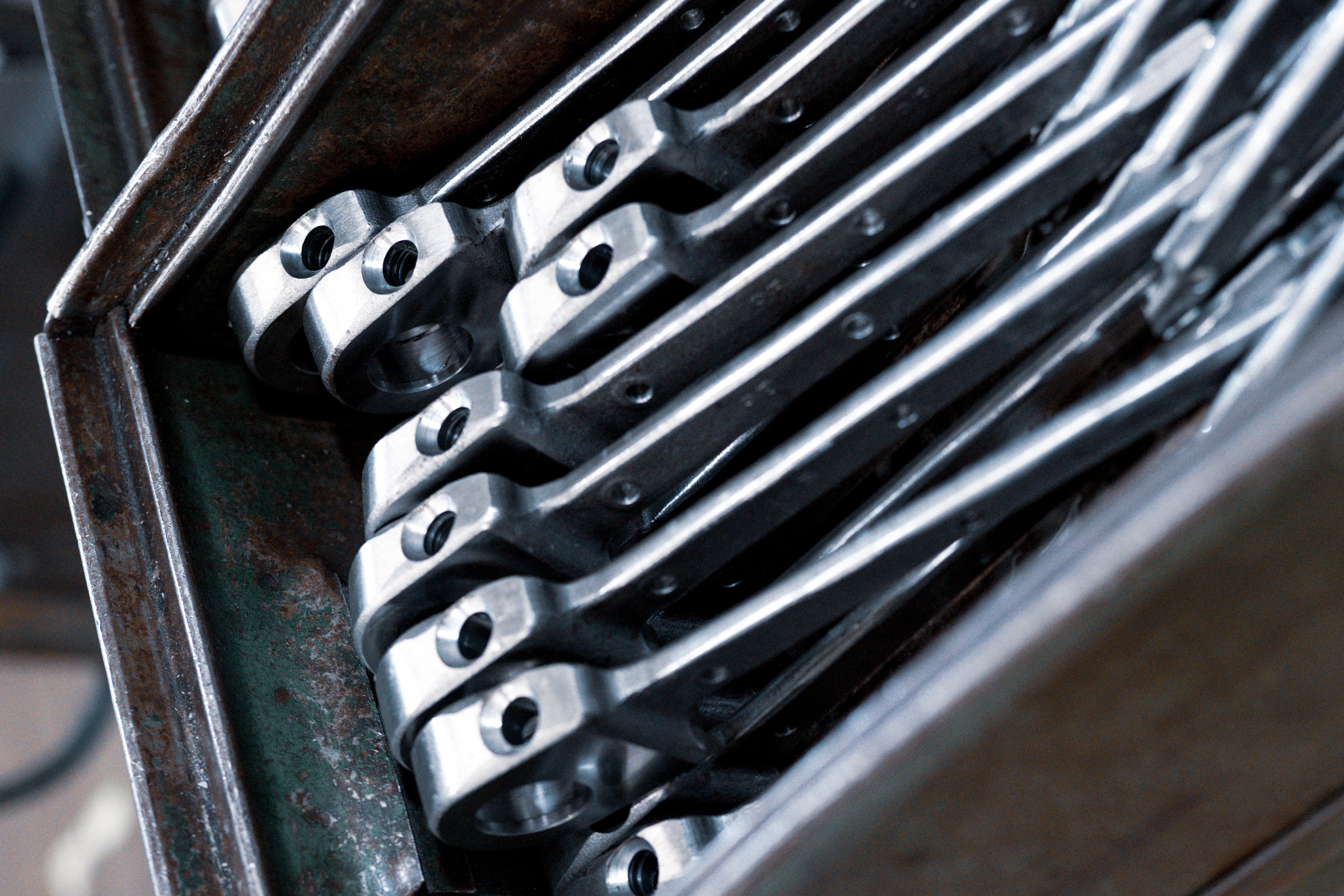
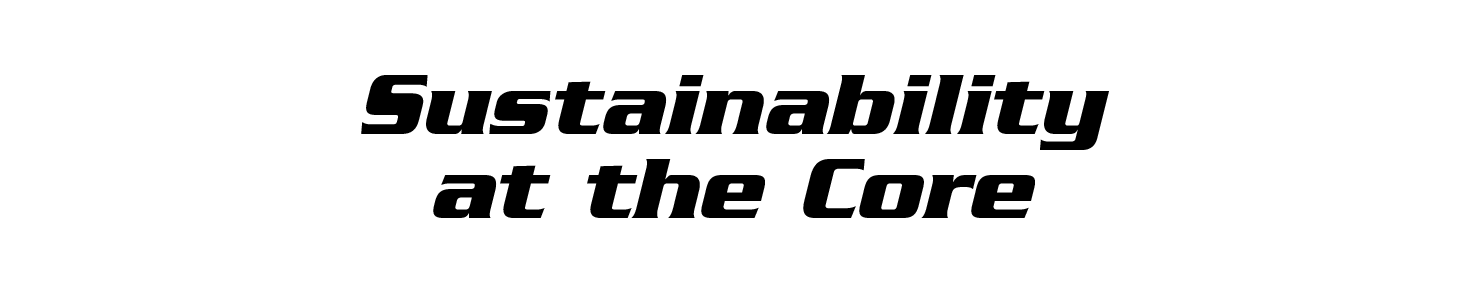
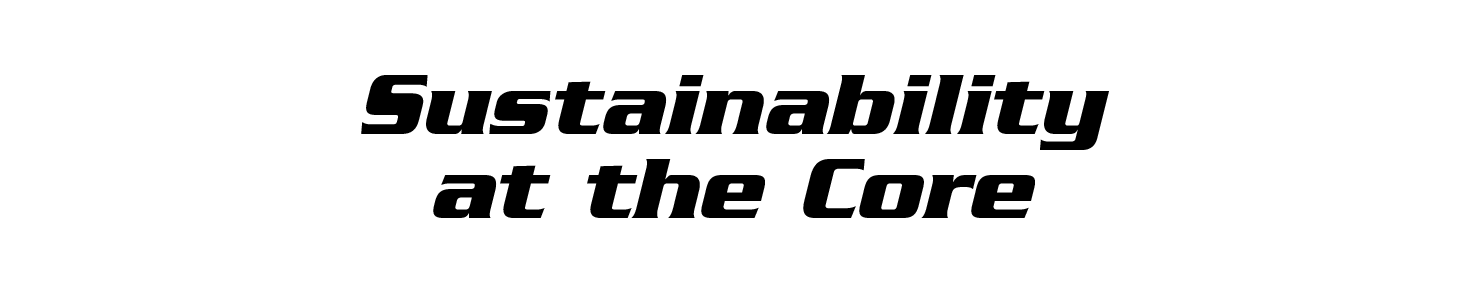
We prioritize environmental sustainability by using Trivalent Chrome, implementing longer chrome plating processes, and recycling throughout our operations. Our rechargeable NiMH batteries provide longer life and are environmentally friendly, aligning with our dedication to reducing environmental impact.
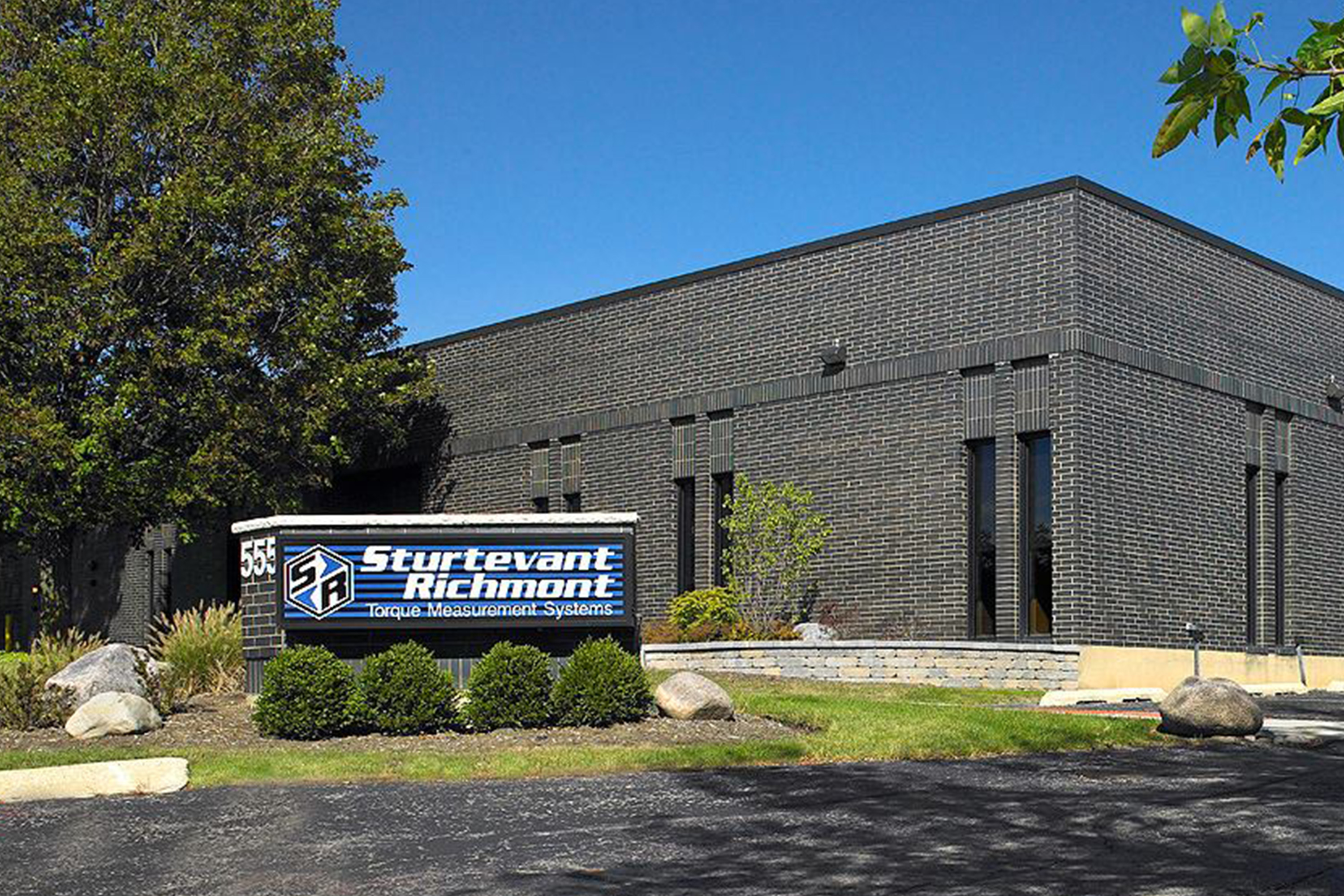
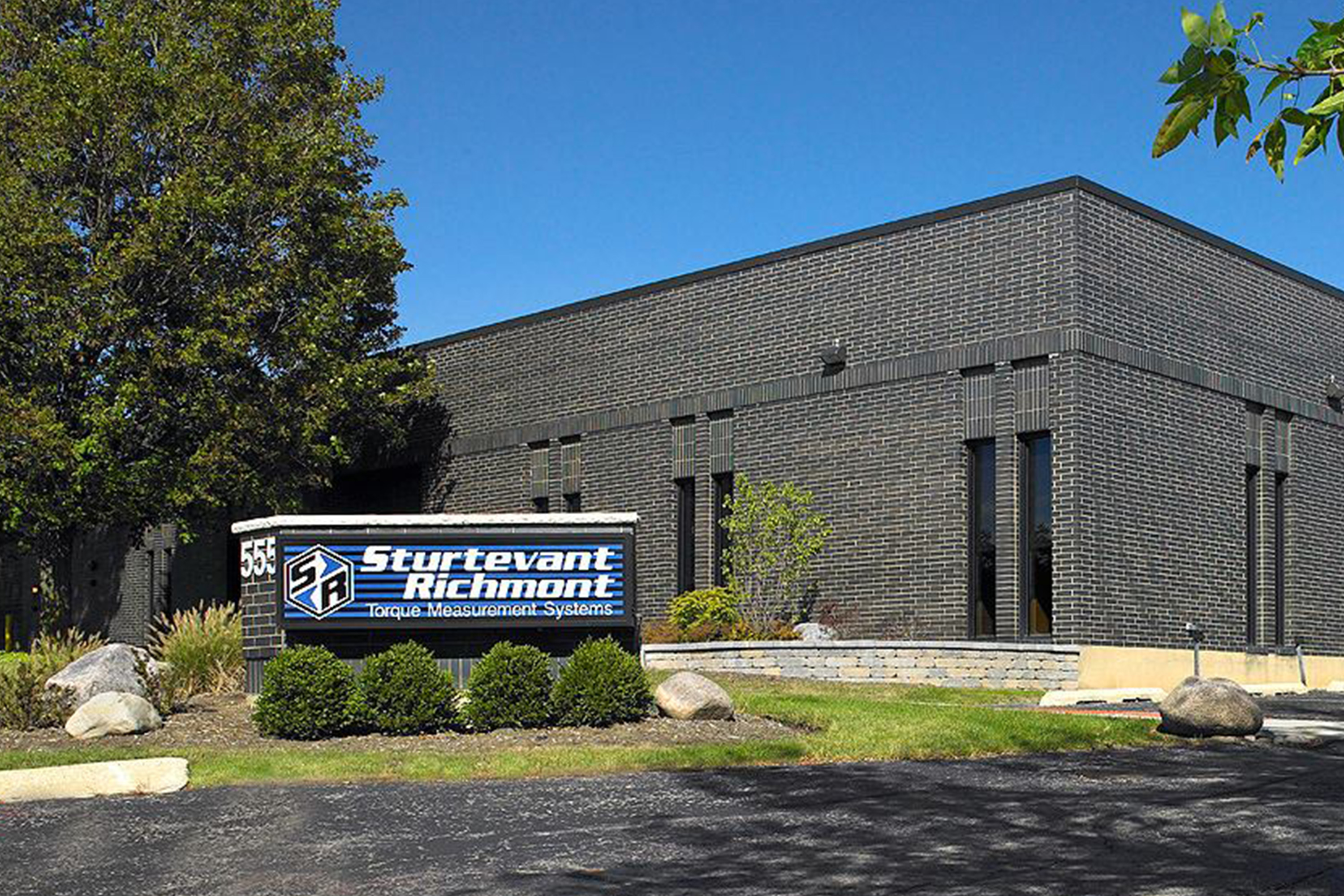
Carol Stream, IL:
our home base
Located in the heart of Carol Stream, IL, just outside Chicago and near Wisconsin, Sturtevant Richmont provides high-quality torque tools trusted by industries worldwide. With a strong network of U.S. and global distributors, we deliver reliable, high-performance tools designed to ensure safety, accuracy, and efficiency in every assembly. Partner with us today for tools that meet your needs, backed by expert service and global support.
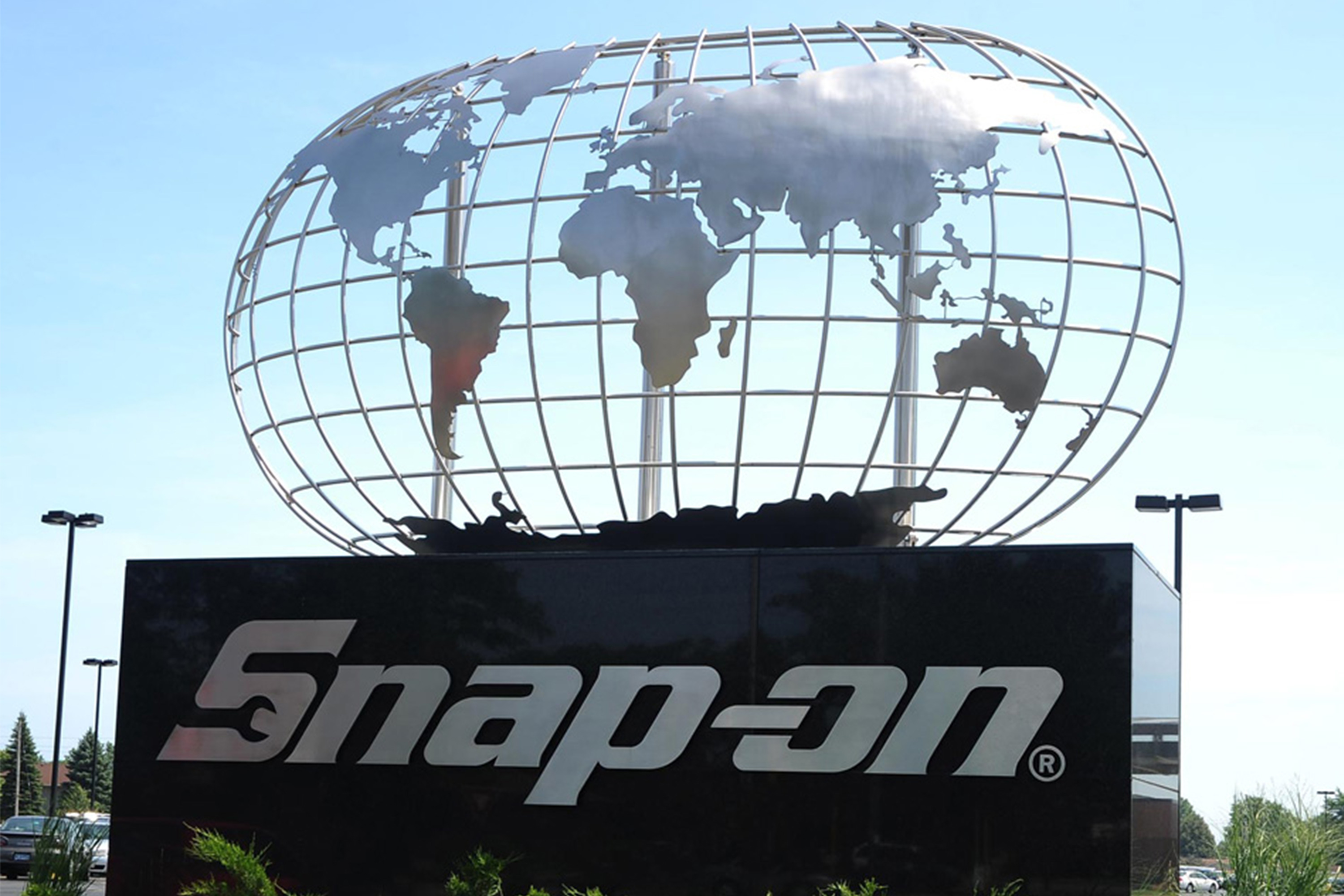
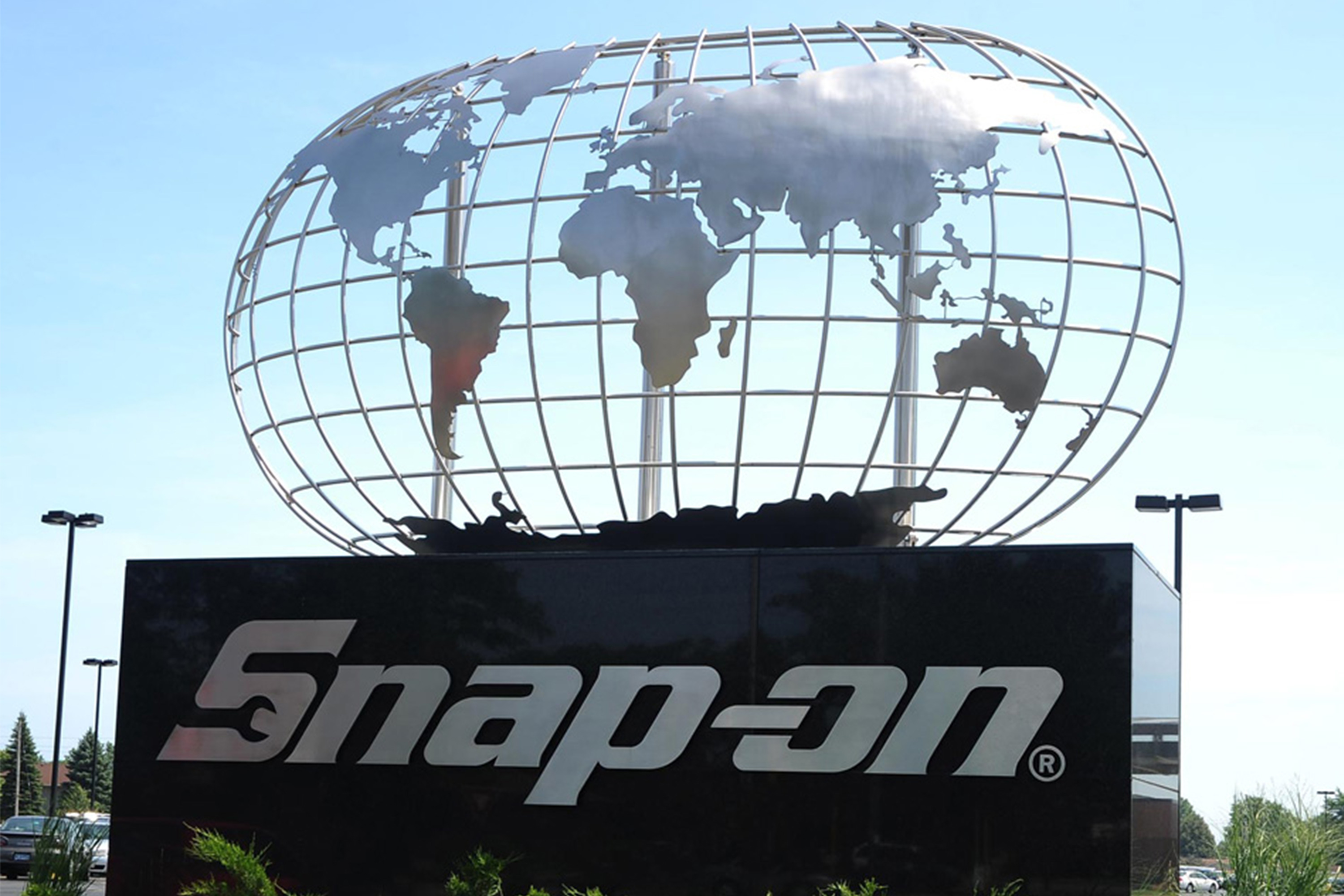
Snap-on:
our parent company
Snap-on Incorporated is a global industry leader in designing, manufacturing, and marketing tools, equipment, diagnostics, and systems solutions for professionals engaged in critical tasks. Their comprehensive range includes hand and power tools, tool storage, diagnostics software, information systems, and equipment tailored for various industries such as automotive, aviation, agriculture, construction, government, military, mining, natural resources, power generation, and technical education.
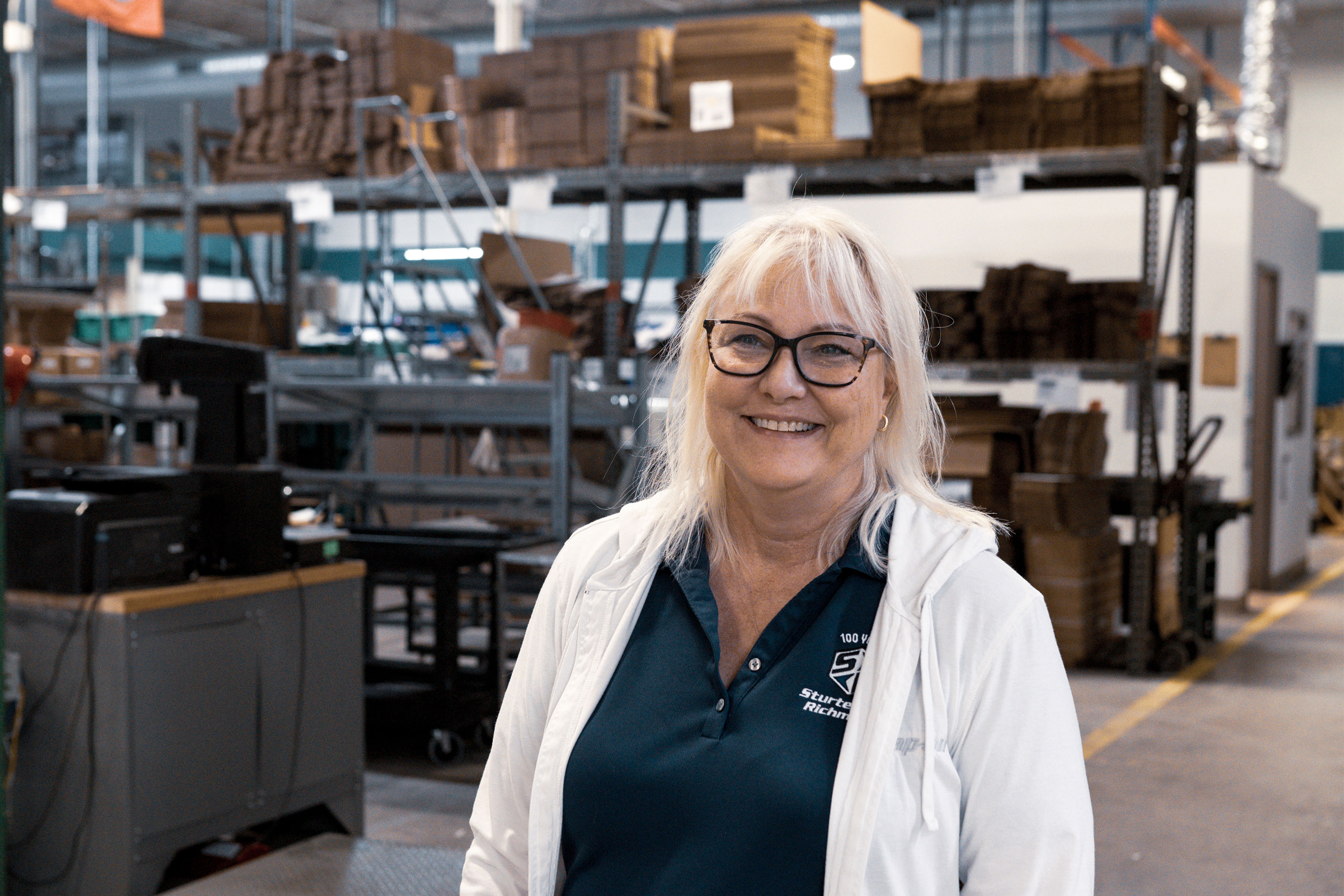
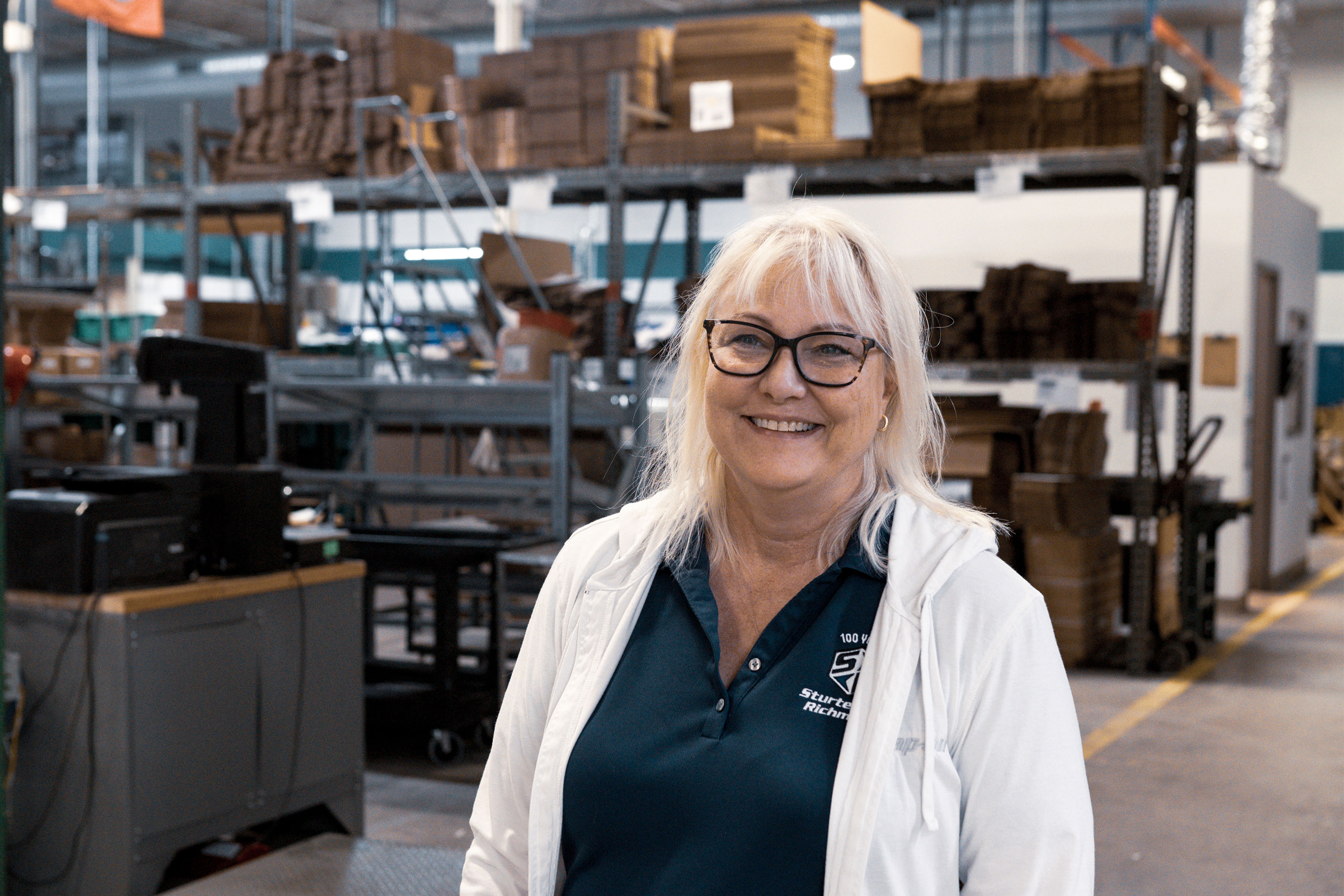
Join the team:
build your future with us
At Sturtevant Richmont, we believe our success starts with our people. We're always looking for passionate individuals to join our team. Whether you're in engineering, sales, manufacturing, or customer support, you'll find a collaborative environment where your ideas are valued and your growth is supported. If you're ready to make an impact and work with a team committed to excellence, explore career opportunities with us today!
We systematically make complex assembly challenges simple.
Our decades of dedication to industrial assembly and deep customer relationships have positioned us as torque experts, driving innovation in torque application. We are committed to quality, implementing advanced error-proofing systems to ensure precision and reliability in every tool we produce.
Accurate. Reliable. Durable.
We strive to embody a relentless pursuit of quality and environmental respect while instilling durability in the core of our operations.
Through our commitment, we craft torque tools that foster workplace safety, elevate the quality of our customers' torque-related assemblies, and drive enhanced assembly throughput.
Our purpose is clear - to deliver tools that are accurate, reliable and durable.
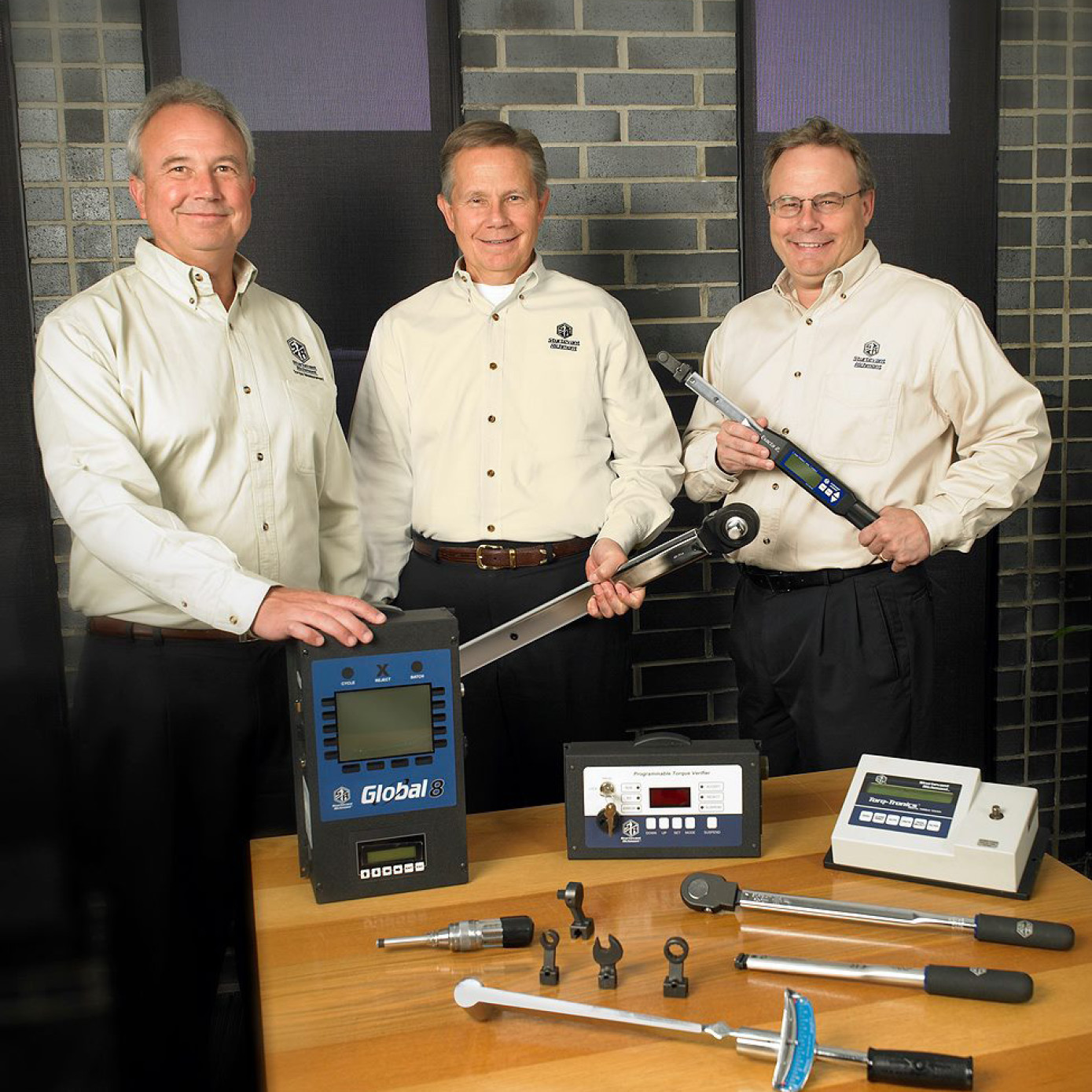
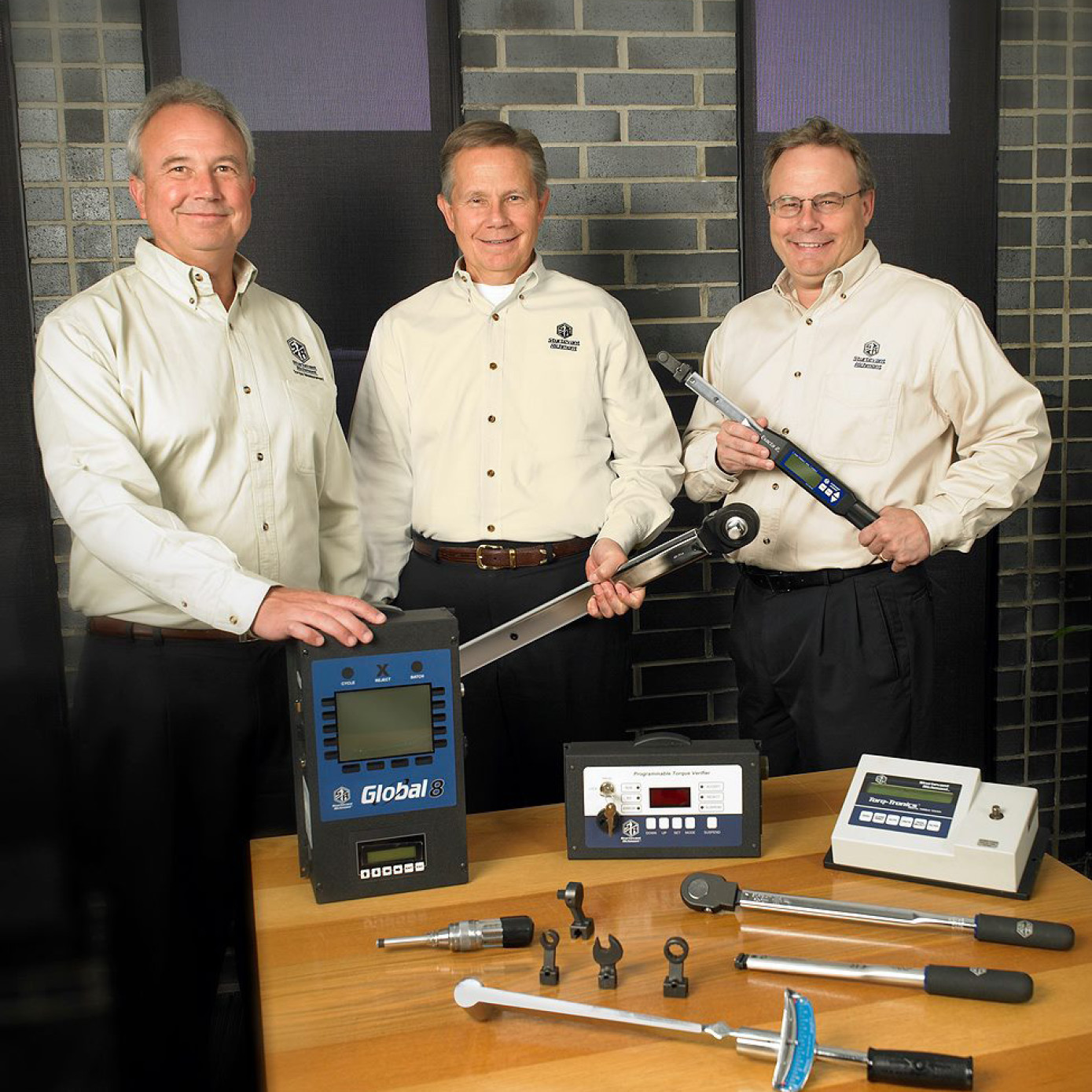
Our business is built on a foundation of deep values, focusing on the quality of our torque hand tools, wireless torque systems, and calibration equipment, as well as our commitment to our customers.
Long-term relationships are central to our ethos. Many of our customers, who first bought from us over 90 years ago, continue to rely on our products today. Similarly, several of our global distributors have been with us for generations, with their children and grandchildren now leading the companies that once partnered with their parents.
We firmly believe that our team strives for excellence every day, and we extend this belief to your operators as well. Our mission is to provide the tools they need to excel in their roles and showcase the quality of their work.
The majority of our employees have been with us for over 25 years, and they continue to come to work each day with genuine enthusiasm and a smile. Their dedication to their work is evident - they don't just excel at their jobs; they are exceptional individuals who care deeply about the quality of our tools and the satisfaction of our customers.
The team is not only intellegent and hardworking but also passionate about what they do. With decades of experience, they possess a keen eye for quality and are adept at identifying when something meets their high standards or needs improvement. They continuously generate innovative ideas and find better ways to enhance our processes.
We are proud to have second and third generation employees who, while not part of ownership, are integral to our daily mission of crafting the world's best torque tools.
For over 40 years, we have expressed our gratitude to our team in various ways, including providing Christmas turkeys. Additionally, our management team hosts a summer picnic where we cook together, enjoy a leisurely lunch, and bond as a team.
Our organization maintains a flat structure with no more than four layers from top to bottom. This close-knit environment fosters deep connections and mutual reliance among all team members, reflecting our strong commitment to each other and our shared goals.
We embraced recycling long before it became a widespread environmental concern, and we continuously strive to enhance our energy efficiency, demonstrating our commitment to sustainability. Our electronics are designed with rechargeable batteries to reduce environmental impact.
Our tools are built to last. For over 40 years, our torque testers have remained accurate, reliable, and durable, eliminating the need for replacements. Similarly, our torque screwdrivers, some over four decades old, still return for calibration.
While our tools may not always be the cheapest, they offer the lowest total cost of ownership due to their accuracy, reliability, and longevity. We hope you'll appreciate our values and choose to partner with us because of what we stand for. We believe that as you get to know us better, you'll recognize the significant value we bring to your company.
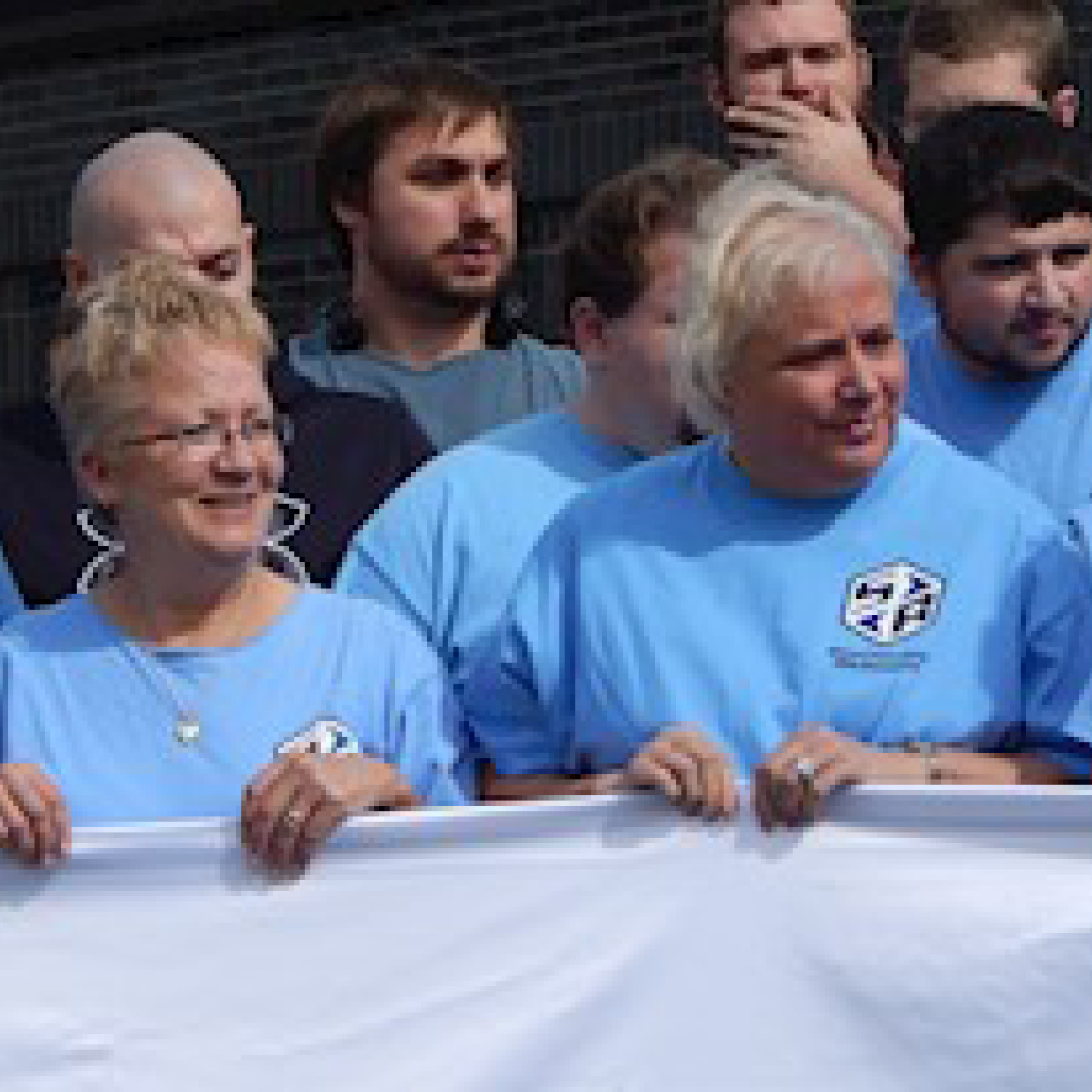
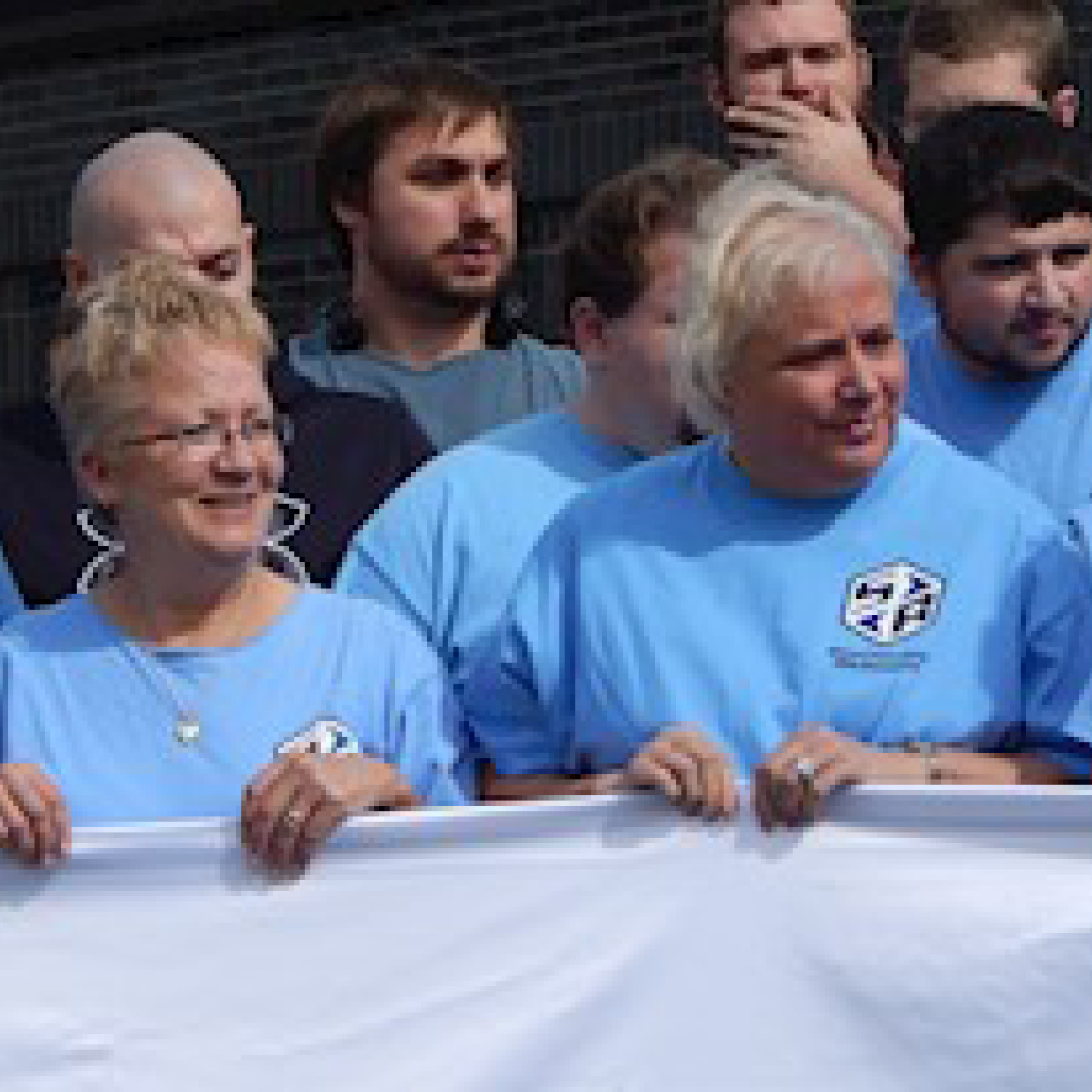
Why choose Sturtevant Richmont?
If you're familiar with Sturtevant Richmont, you know our tools and testers are renowned for their exceptional accuracy, reliability, and durability. Our products are easier to calibrate and maintain their calibration longer than other brands. But what sets Sturtevant Richmont apart?
Relentless Pursuit of Quality
W. Edwards Deming famously said that quality must be built into a product, not inspected in. We wholeheartedly embrace this philosophy, meticulously focusing on every detail to ensure superior quality.
Take a Sturtevant Richmont wrench, and you'll notice its robust feel despite it being so lightweight. This is due to our use of higher-grade steel, which allows us to use less material while enhancing strength.
Our Exacta 2 series wrenches, including the 1100, 1200, and 1250 series, are made from aerospace-grade aluminum. This material not only provides exceptional strength but also can withstand extreme conditions - such as being run over by an SUV or enduring rigorous drop tests.
Another critical design element is the Shear Beam transducer used in our Exacta Series digital torque wrenches. This transducer, housed in a flattened case and guided by eight proprietary steel ball bearings, minimizes level sensitivity issues. The flattened case prevents side loading - torque applied at an angle other than 90 degrees from the fastener - which can distort torque measurements. By maintaining a true 90-degree angle, the Shear Beam design ensures more accurate and reliable torque application.
Commitment to Environmental Responsibility
Before regulations on Hexavalent Chrome were even established, Sturtevant Richmont had already transitioned to using Trivalent Chrome, reflecting our early commitment to health and environmental concerns. We extend this commitment through our chrome plating process, which involves a 96-hour bath - far longer than the typical 24 hours used by most companies. This results in a thicker, more resilient chrome layer that enhances both the appearance and durability of our tools.
Our dedication to the environment is evident in our operations. We have recycled since our inception, conserve water, and use rechargeable NiMH batteries, which offer longer life, stable performance, and environmental benefits. These batteries are also recyclable at the end of their lifespan.
Built-In Durability
Durability is embedded in the design of all our tools. For instance, the CAL 30 Torque Screwdriver, discontinued in 1972, continues to be used and serviced today. We have a customer with 40 CAL 30 screwdrivers still in daily use after 50 years - a testament to our tools' enduring quality. Similarily, our beam wrenches have been a staple on a car company's assembly line since 1993, demonstrating our tools' long-term reliability.
Proven Performance
In 1968, a NASCAR team purchased one of our torque testers. When they contacted us in 2013 for new TorqTronics 2 units and additional torque wrenches, they offered to return the old tester. Upon inspection, we found it still met tolerance standards after 45 years of service. Despite its continued functionality, the team upgraded to newer models for improved accuracy and space efficiency, with the new TorqTronics 2 units offering a superior accuracy of +/- 0.5% comparted to the old tester's +/- 1%.
This enduring performance and the tangible return on investment highlight why our tools are renowed for their durability.
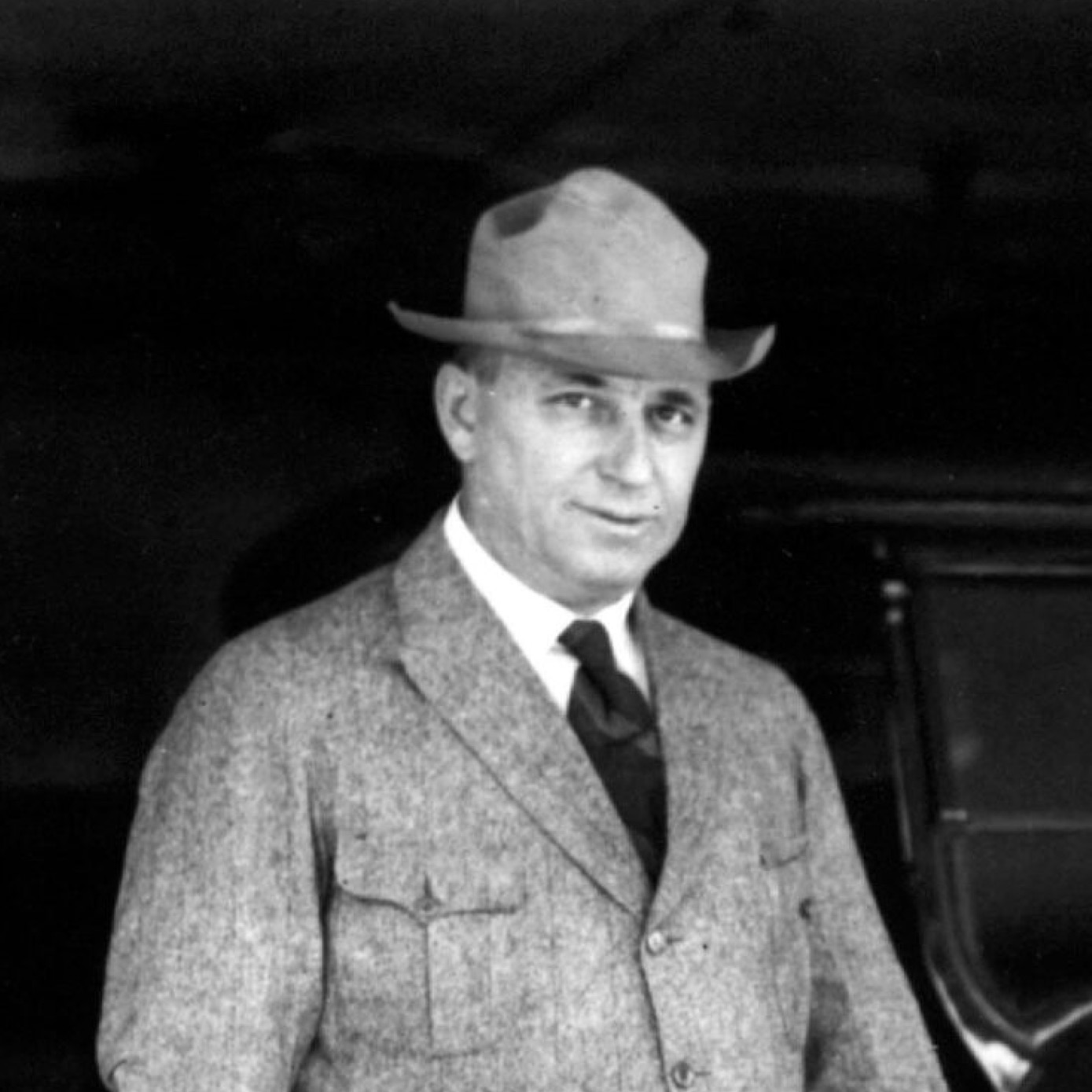
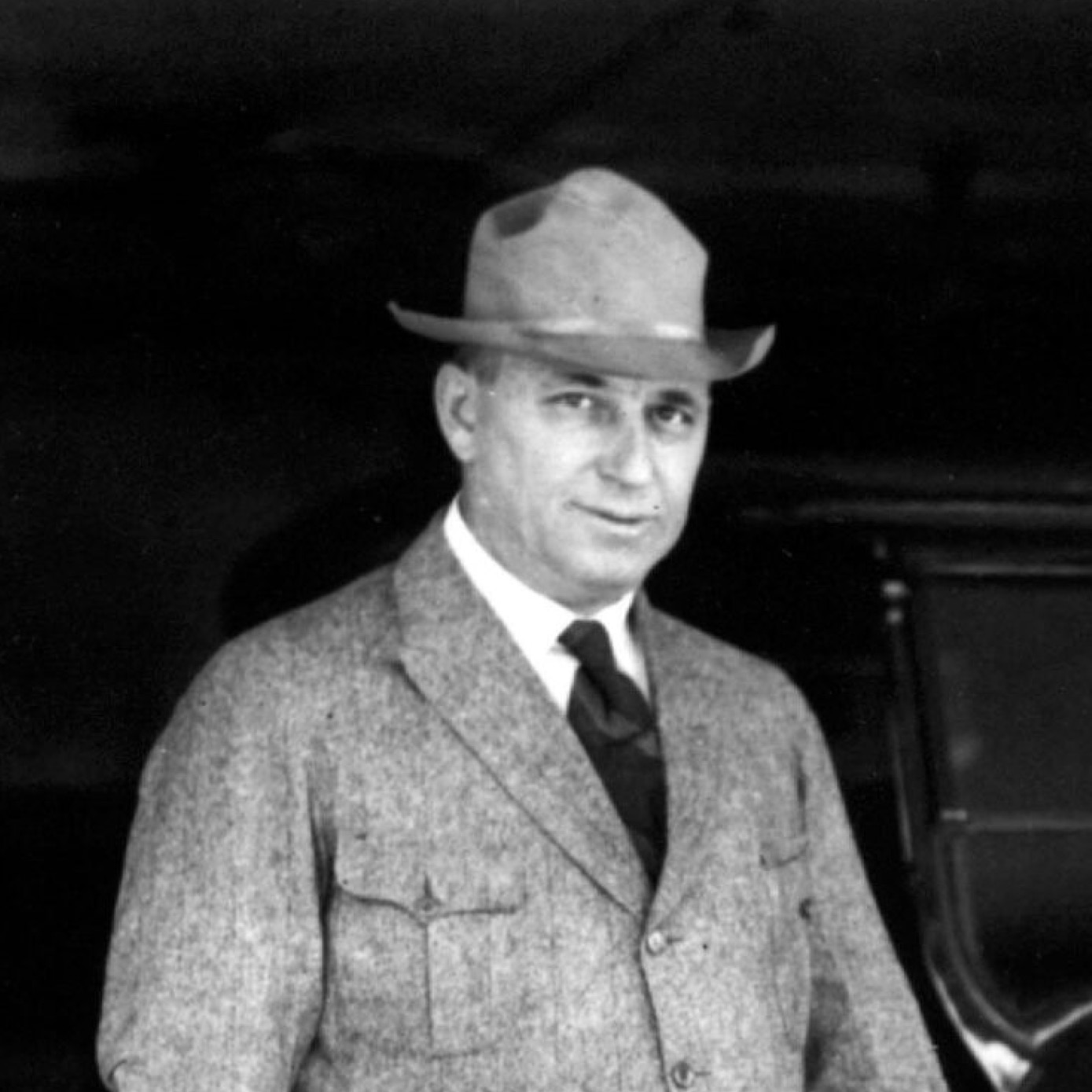
1924
Walter P. Chrysler invents the beam Torque wrench and licenses Paul Sturtevant to manufacture and sell it.


1940
Paul Sturtevant incorporates the PA Sturtevant Company and Frank W. Livermont incorporates Richmont, Inc.
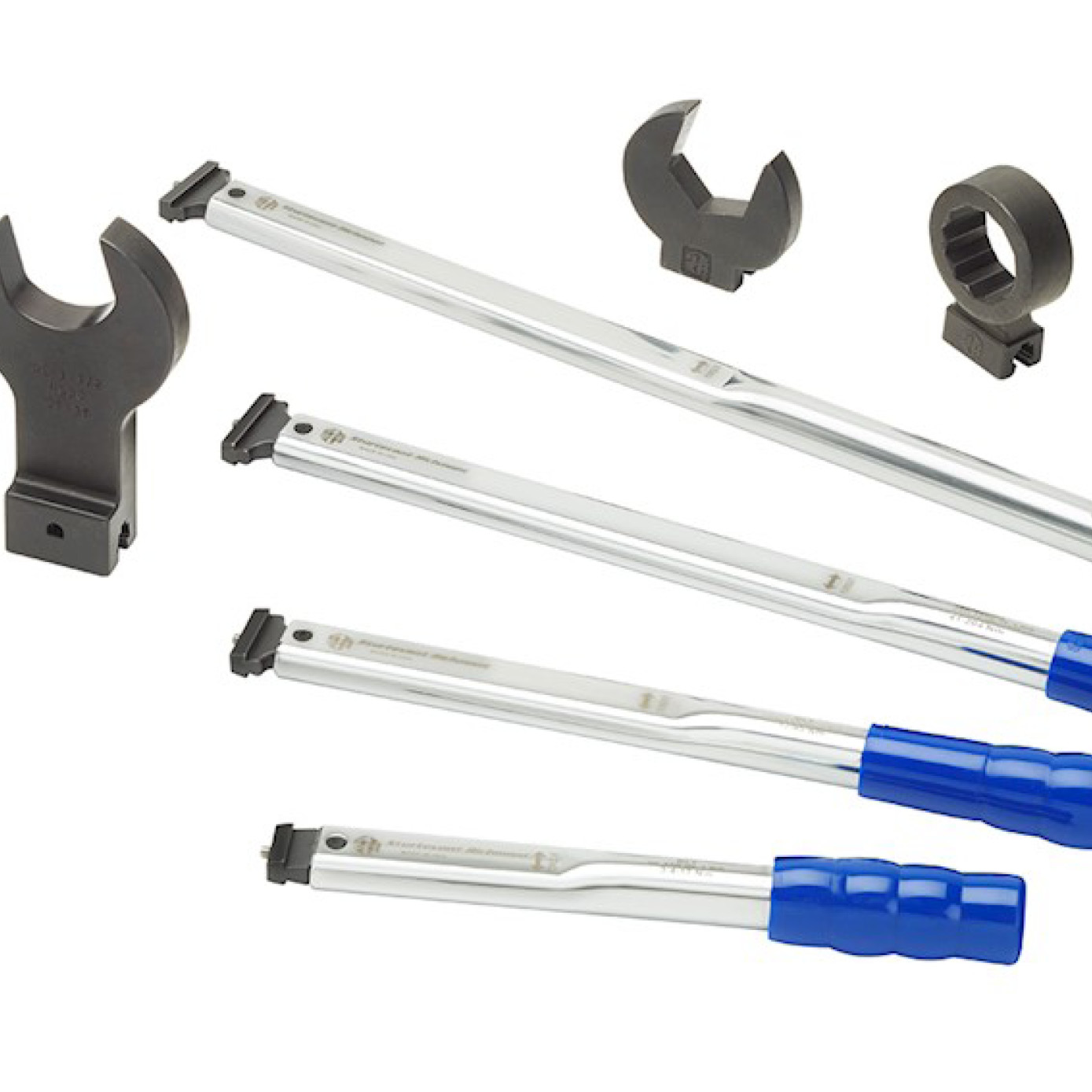
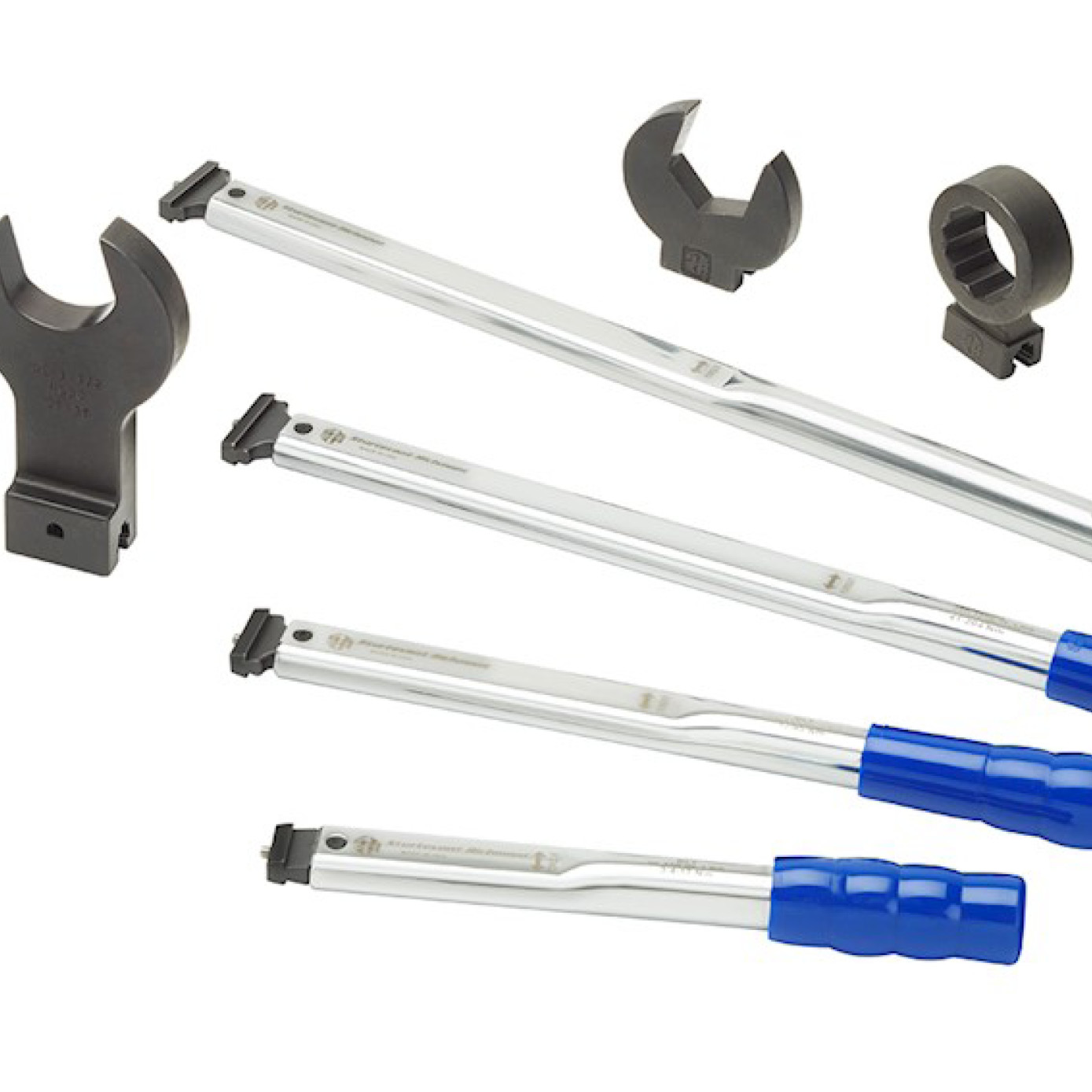
1958
Livermont awarded the patent for interchangeable heads for torque wrenches. Patent US2832246.
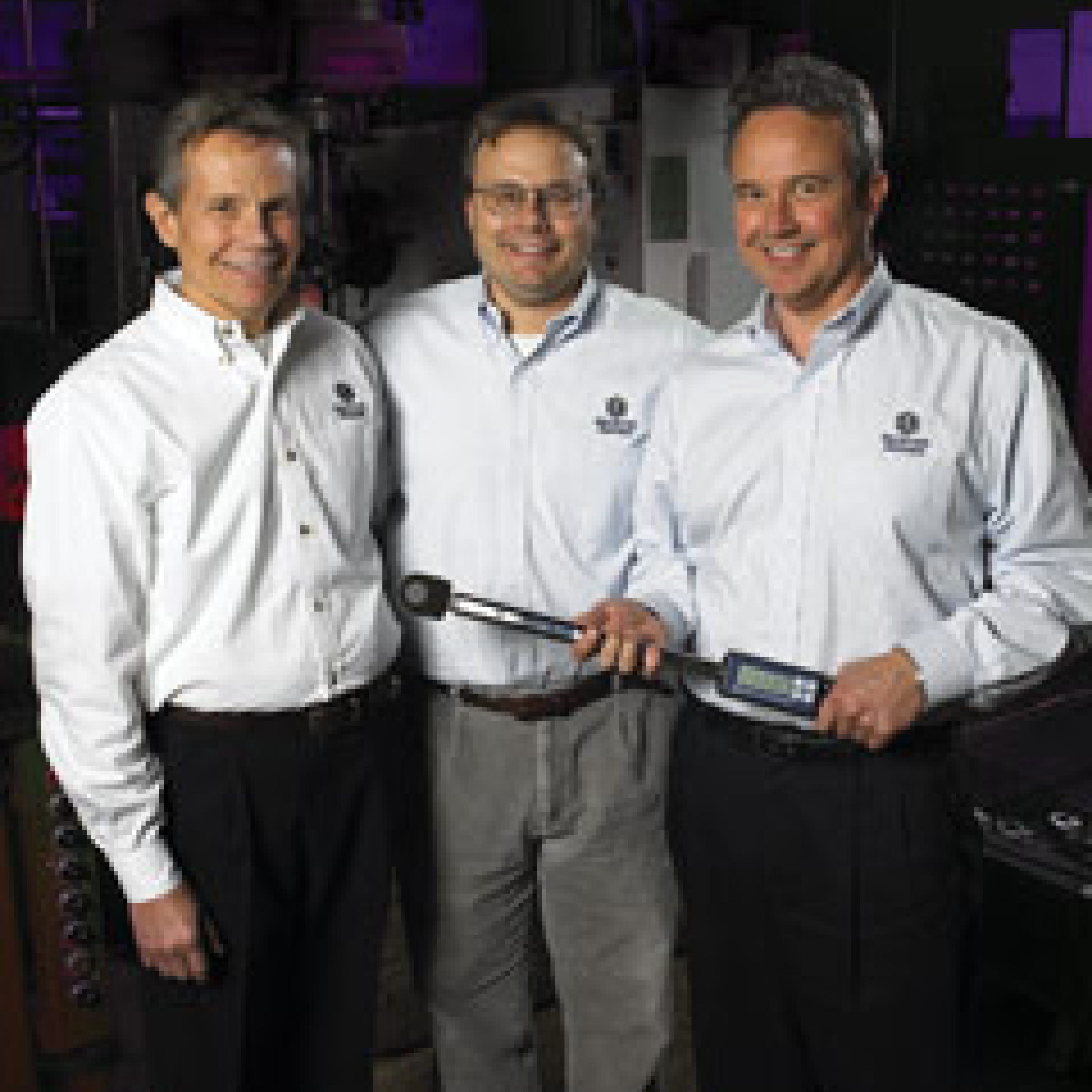
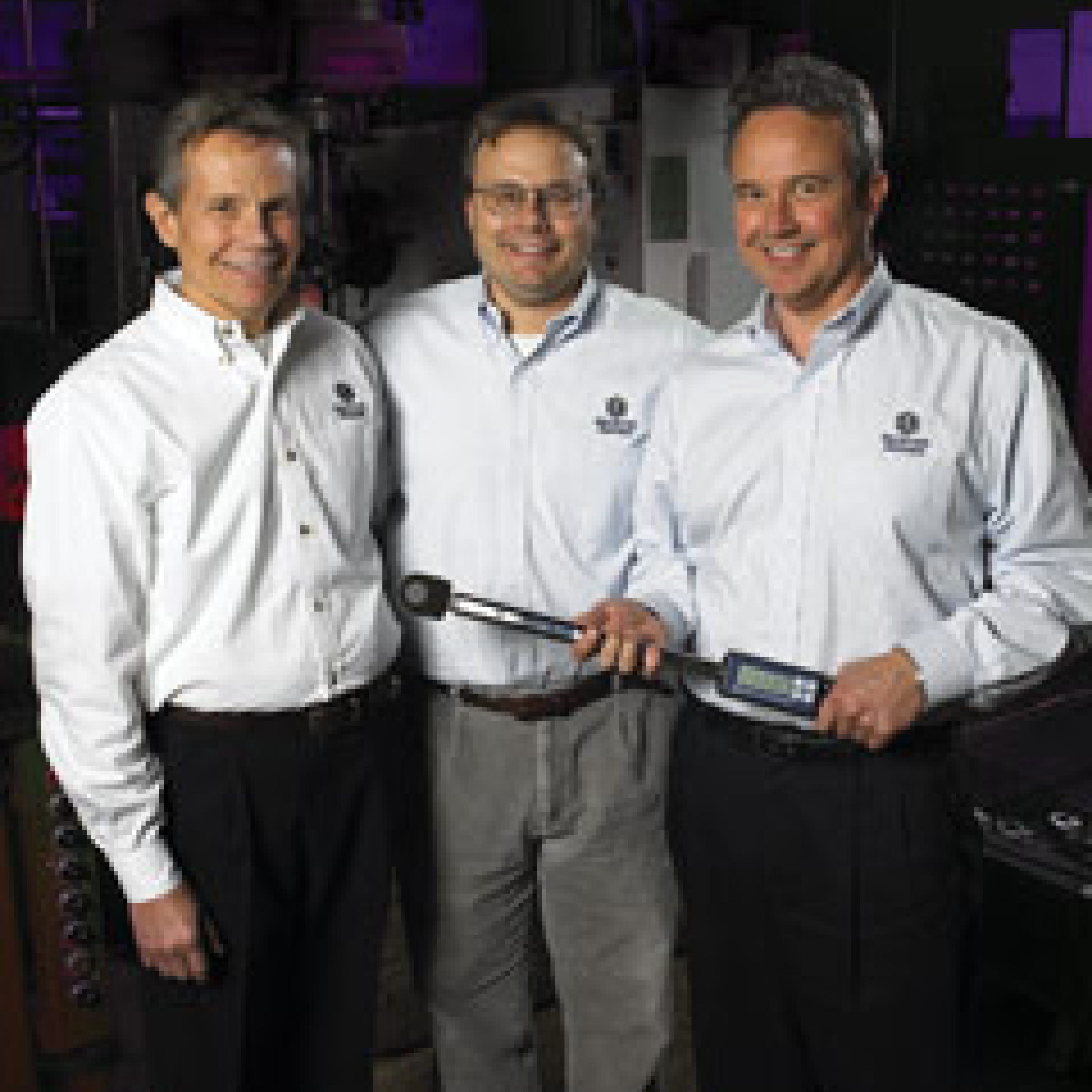
1971
Jack Reynertson merged Sturtevant Richmont together to form the world's most comprehensive torque tool product line.
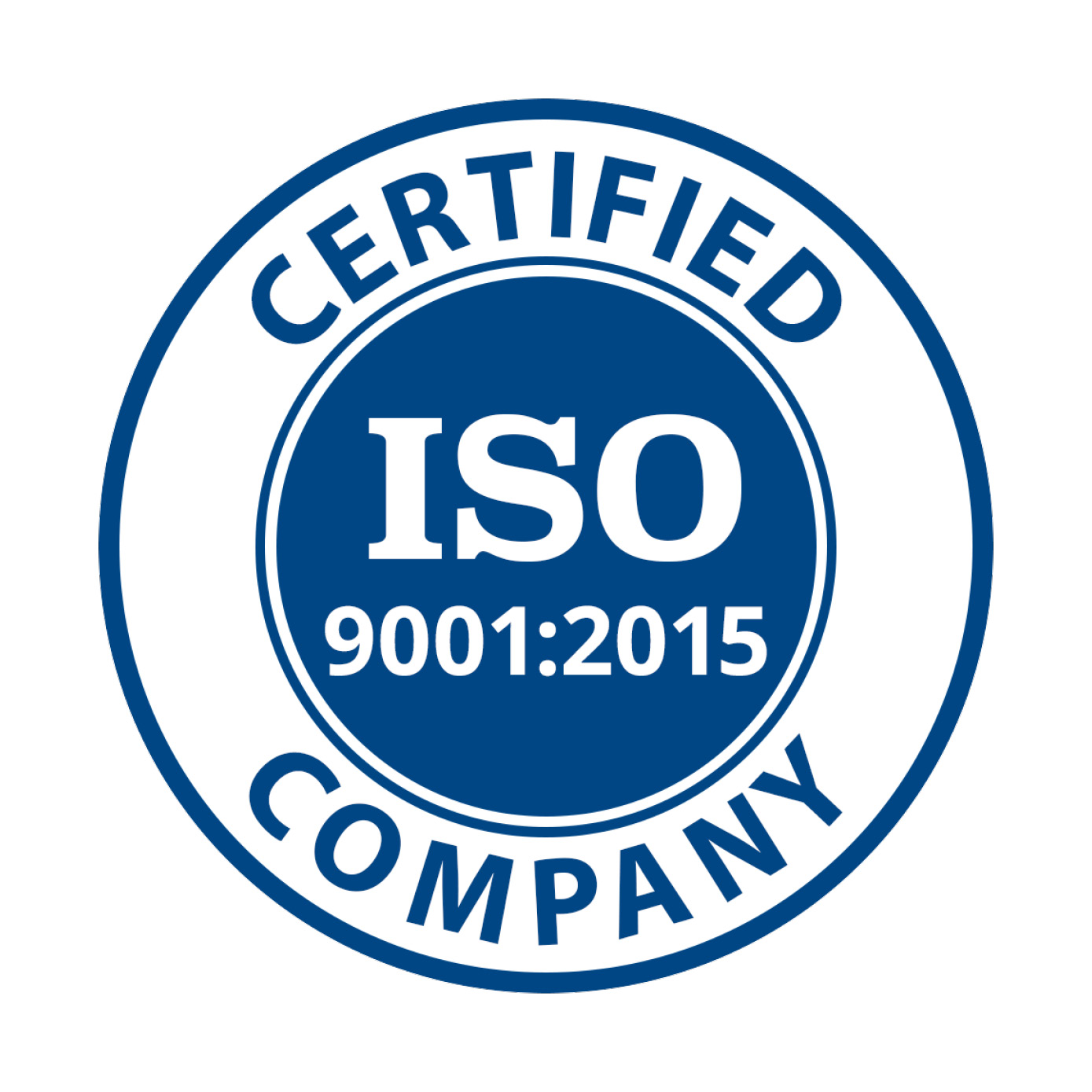
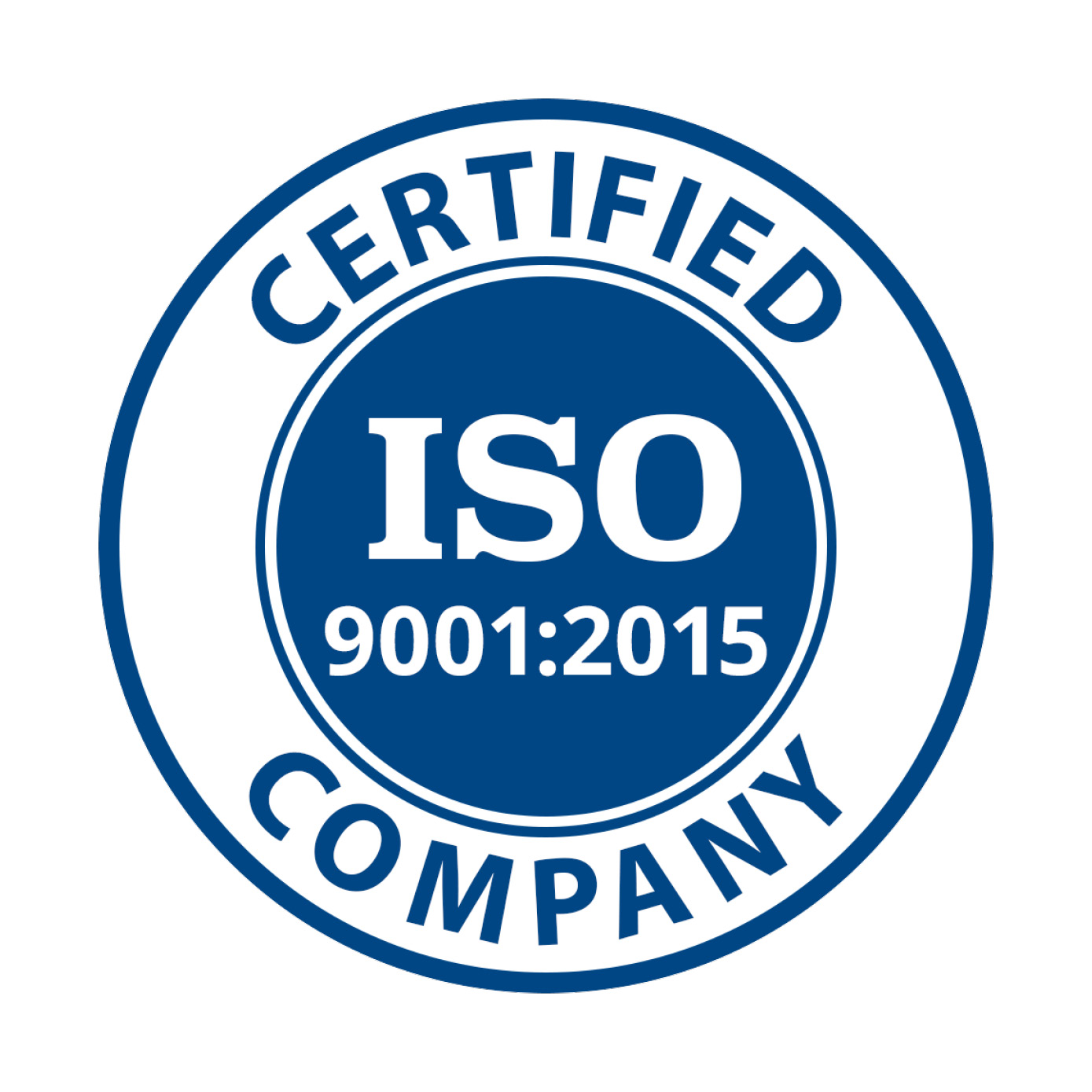
1994
Sturtevant Richmont is the first torque tool company to become ISO 9001 certified.
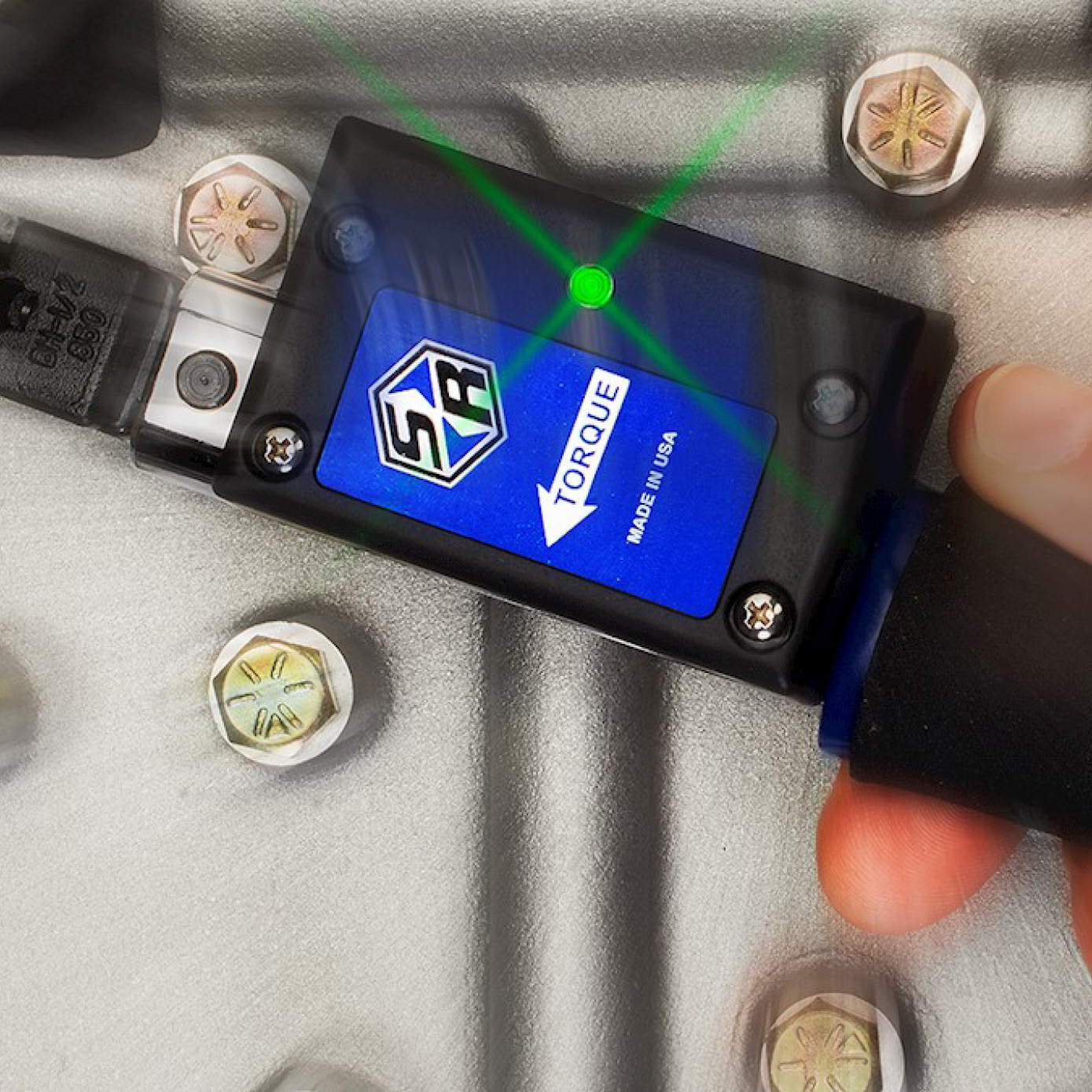
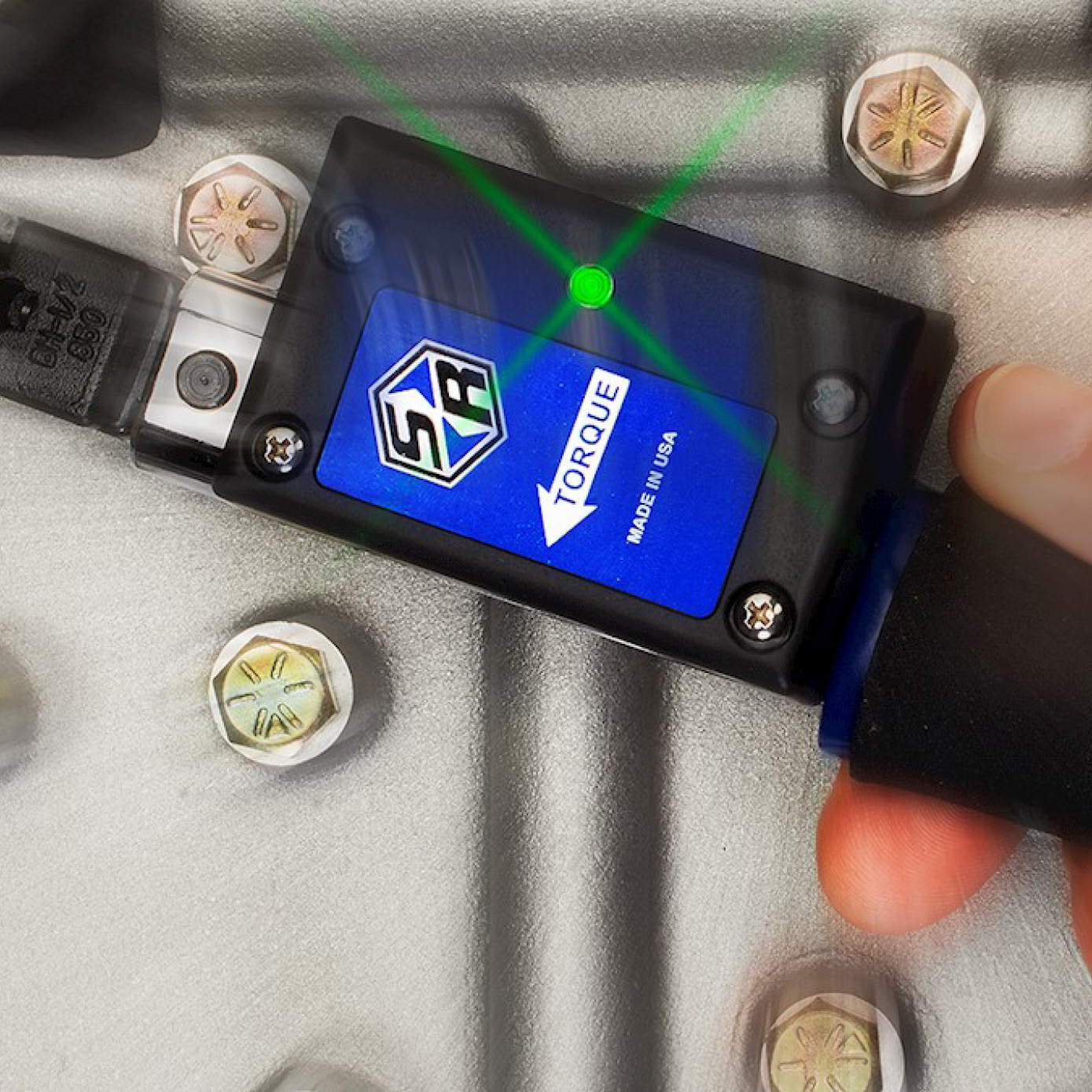
1999
Sturtevant Richmont is the first to manufacture and market the wireless radio equipped 900MHz click wrench that communicates with a process monitior, the PTV.
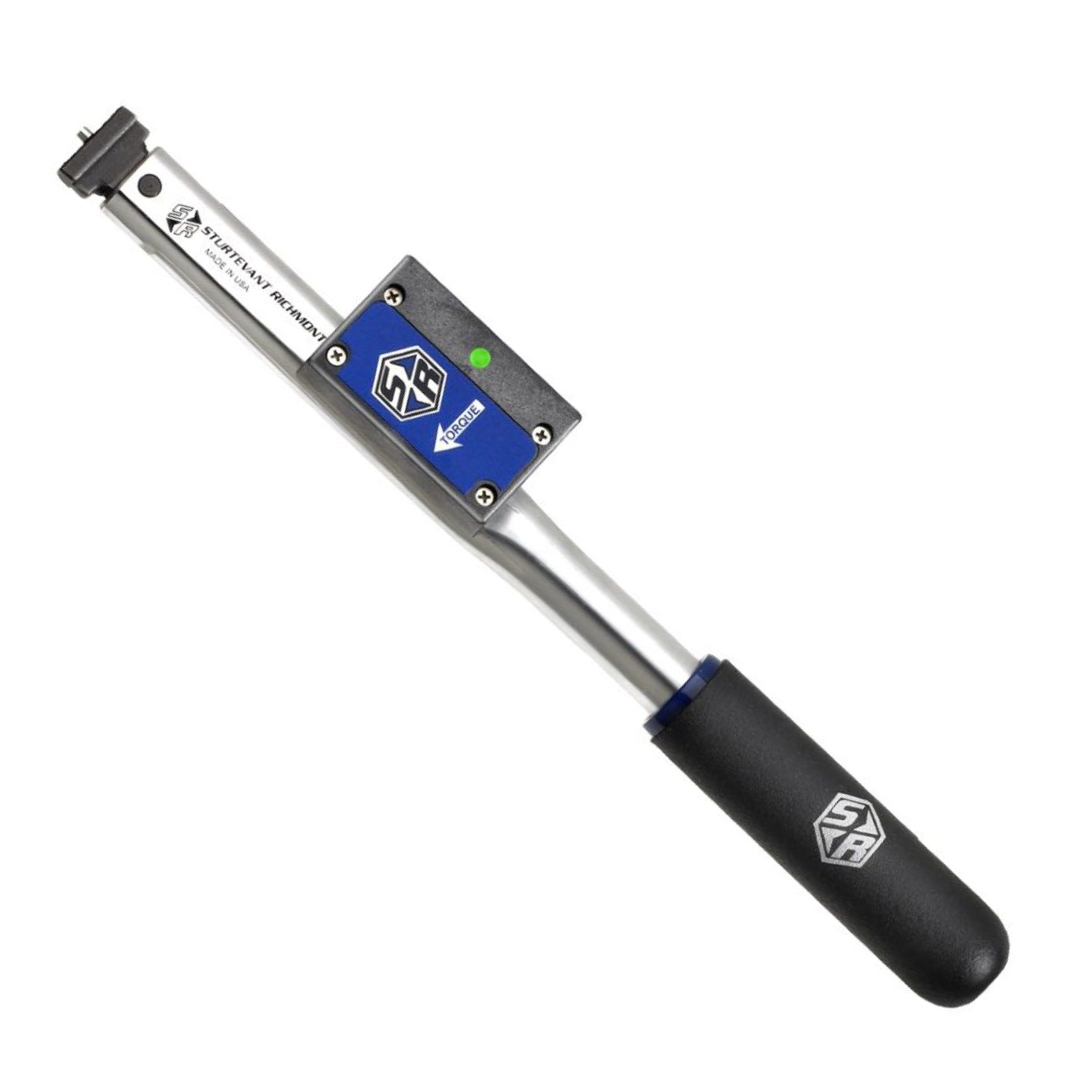
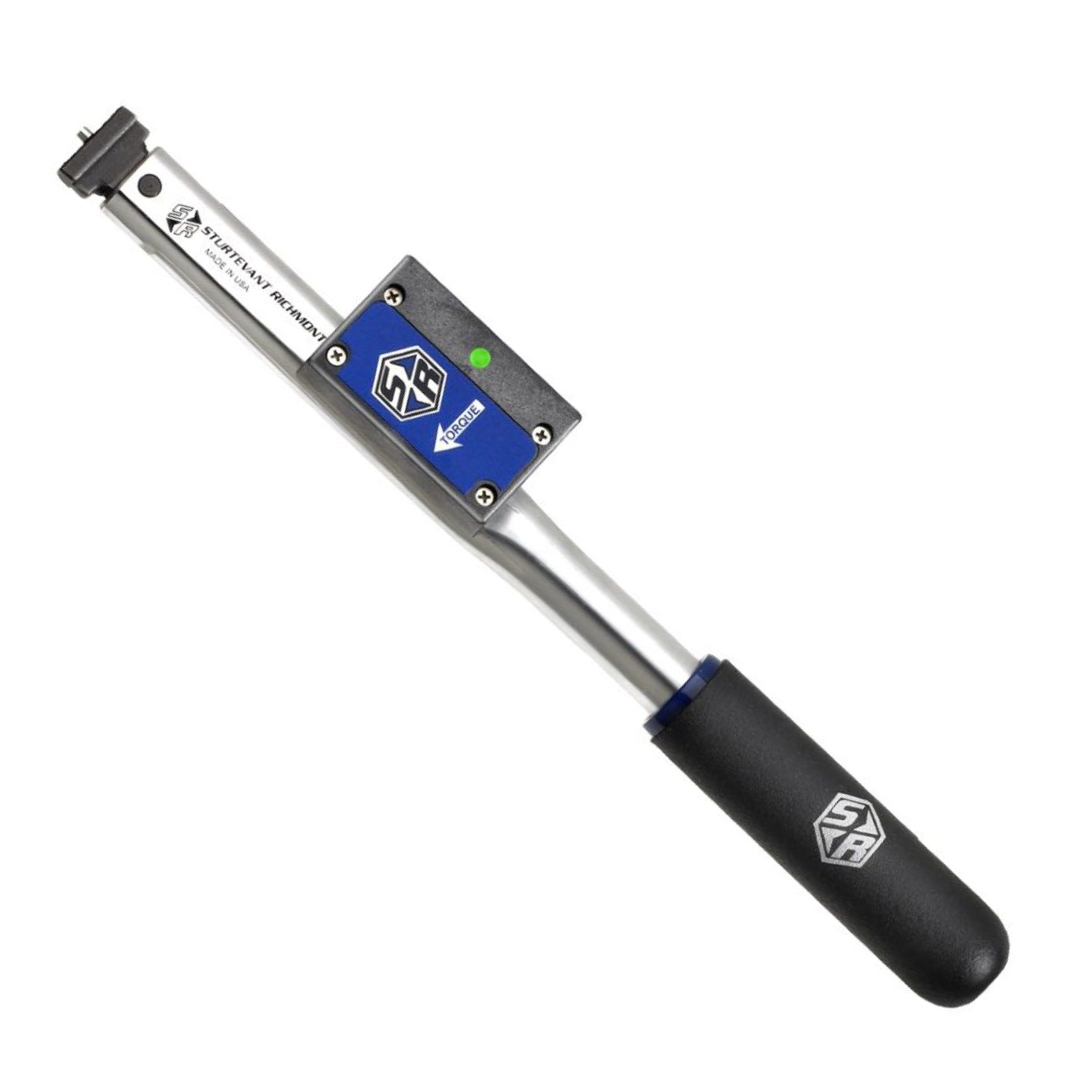
2005
Introduction of the SLTC FM 2.4 GHz Click Wrench.
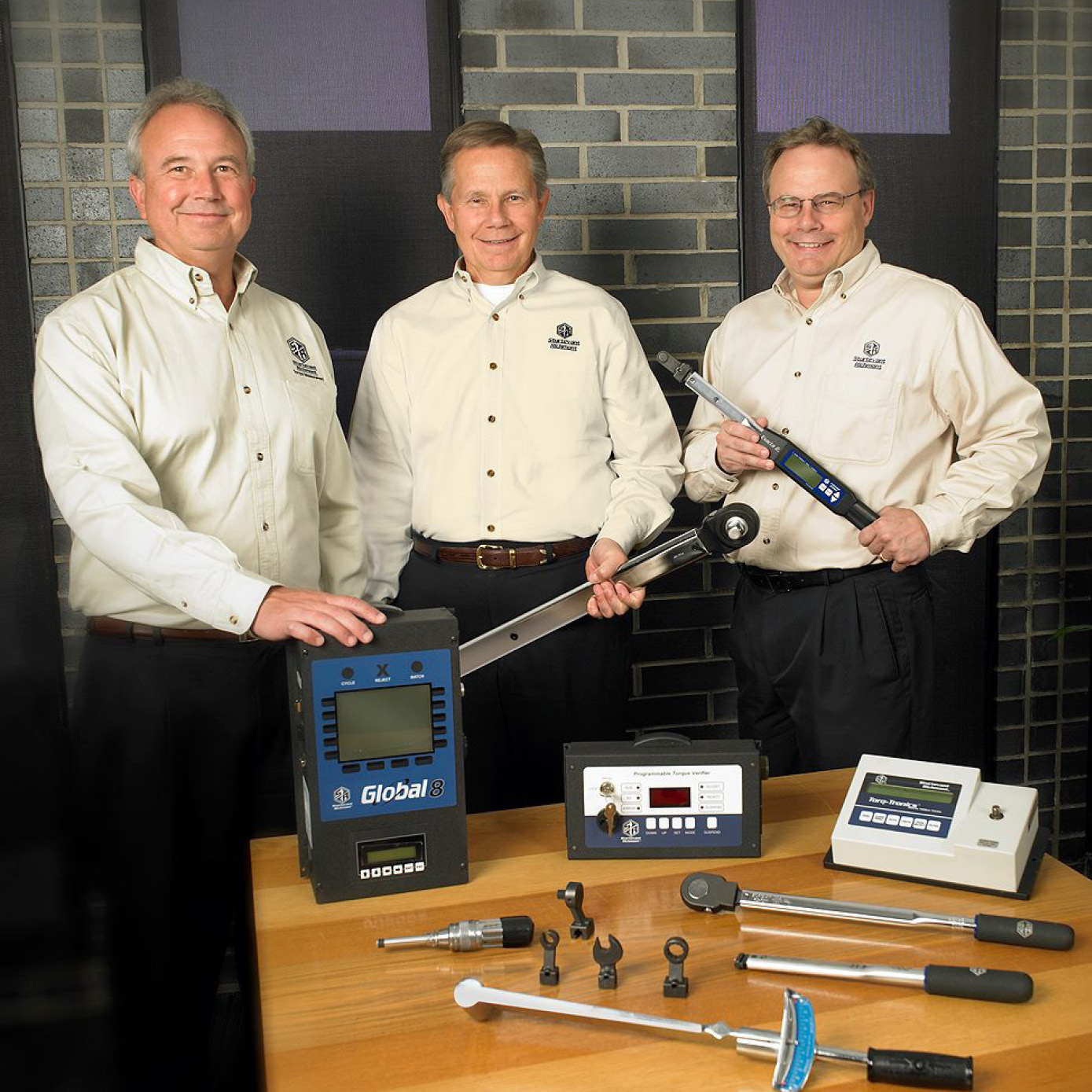
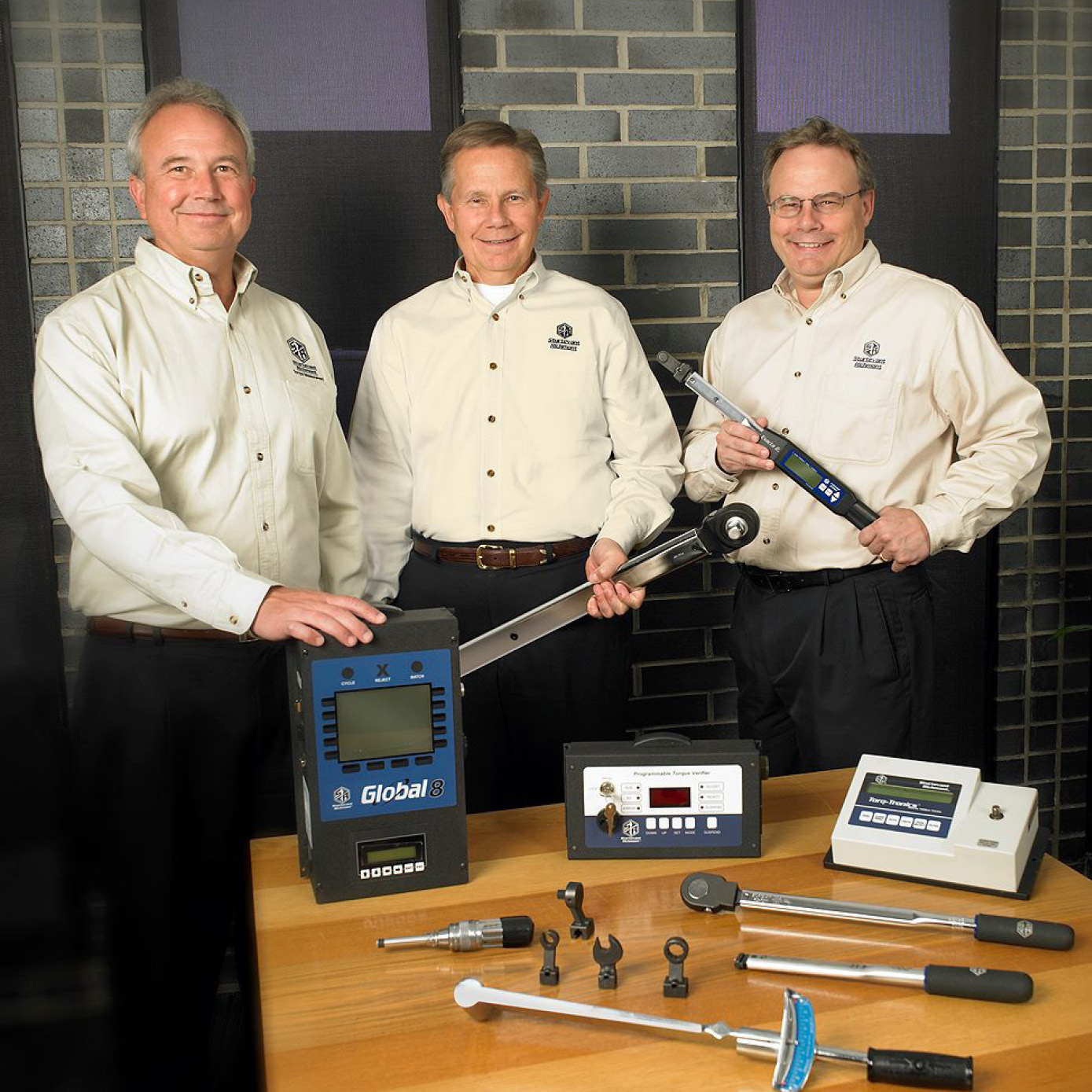
2014
Sturtevant Richmont recevies UL Award for 20 Years of Excellence and ISO Certification.
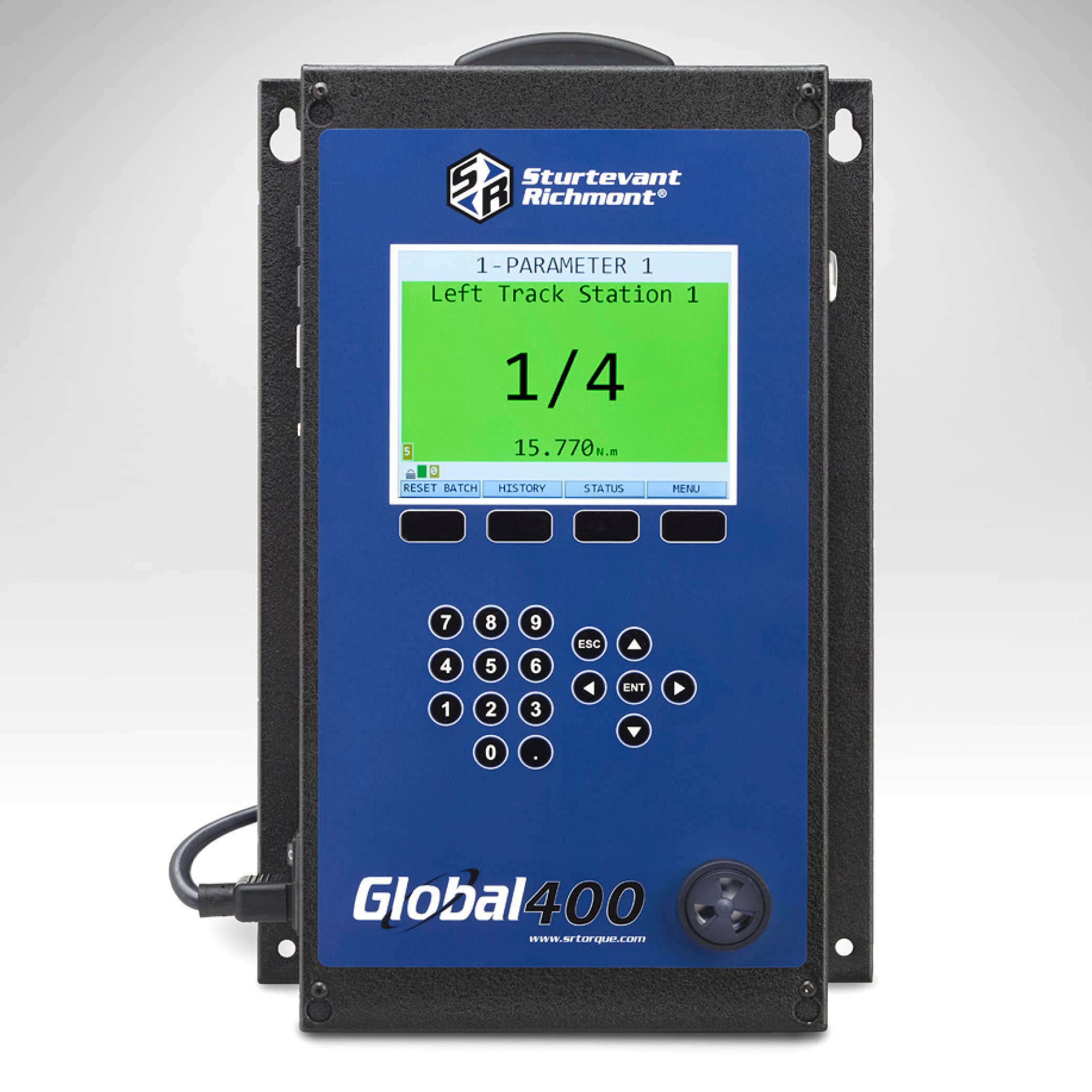
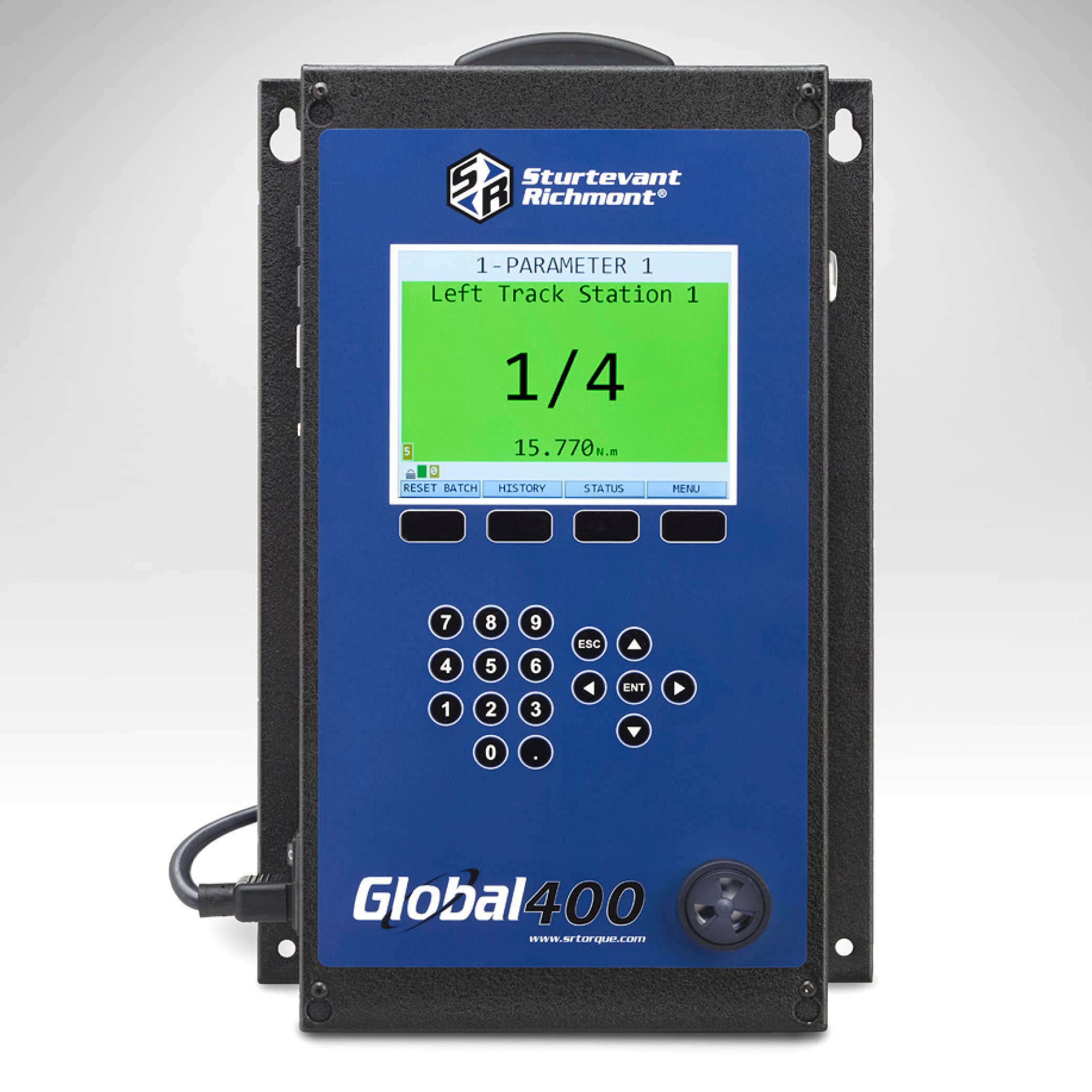
2016
Introduction of the Global 400® Torque Proccess Monitoring System.
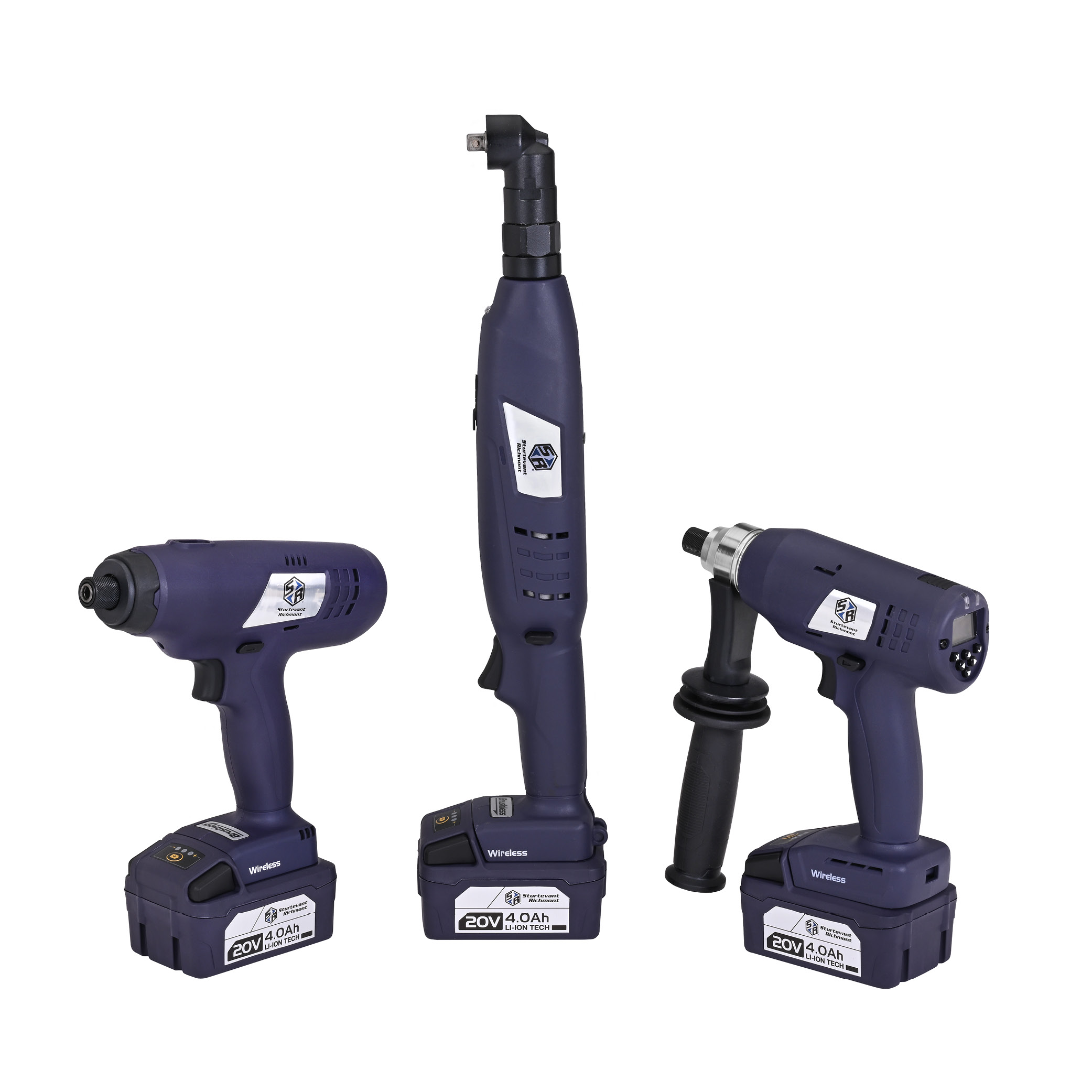
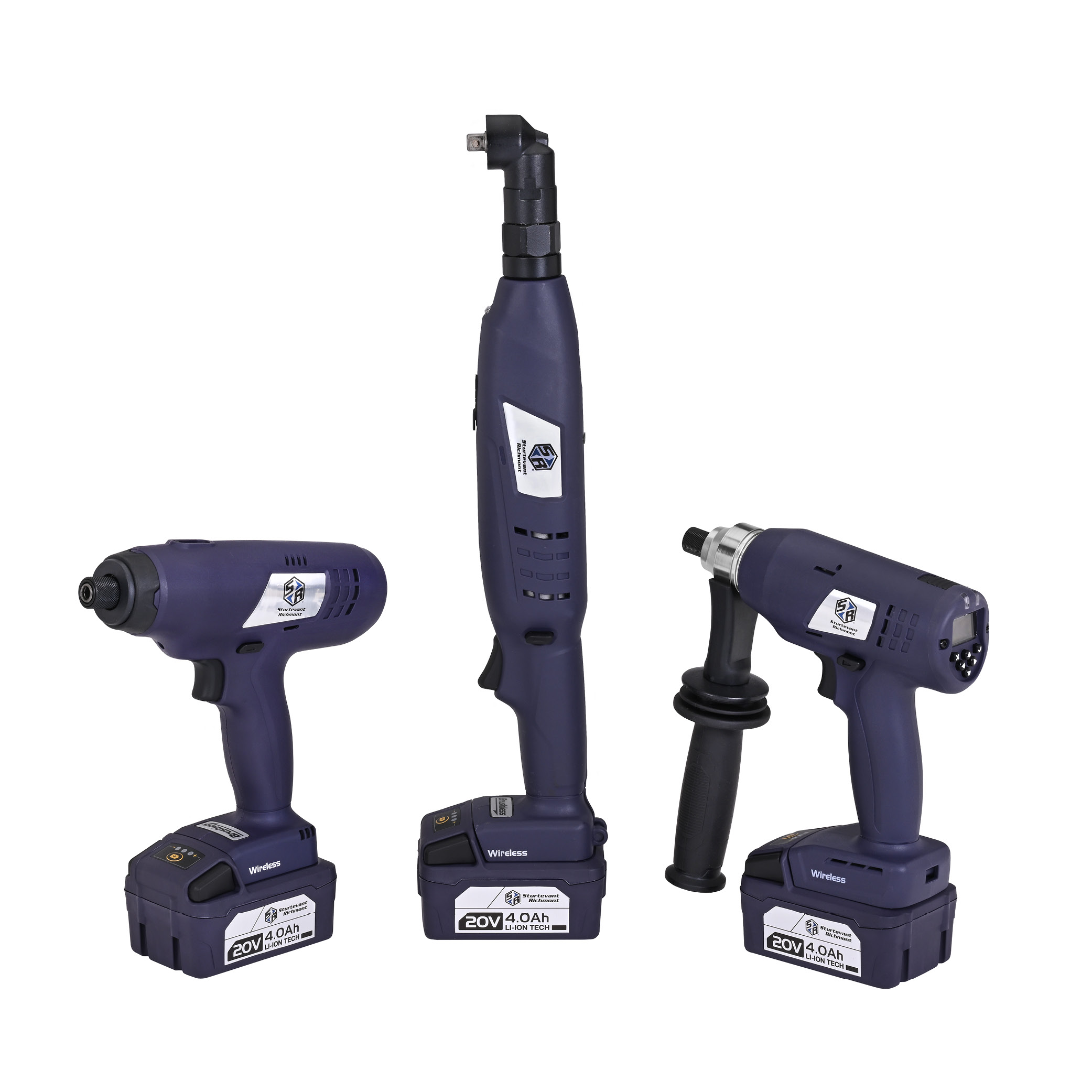
2024
Introduction of Sturtevant Richmont Connected Power Tools.


OUR PARENT COMPANY
Snap-on Incorporated is a global industry leader in designing, manufacturing, and marketing tools, equipment, diagnostics, and systems solutions for professionals engaged in critical tasks. Their comprehensive range includes hand and power tools, tool storage, diagnostics software, information systems, and equipment tailored for various industries such as automotive, aviation, agriculture, construction, government, military, mining, natural resources, power generation, and technical education.
For full product offerings: snapon.com
For career opportunities: snapon.com/EN/Careers
12,900
ASSOCIATES
WORLDWIDE
130+
COUNTRIES
SERVED
3,600+
ACTIVE & PENDING
PATENTS
80,000+
PRODUCT
LINE SKUS